Safety In Construction Site or Industry
Scope of Safety on Construction Site
Basic Philosophy
- There are huge numbers of firms and workers in construction site in India.
- It is labor oriented and unorganized.
- Workers are mobile, mostly illiterate and work on contract basis.
- They work under sun and rain, cold and wind, dust and sand.
- Working conditions are mostly unsafe, hazardous and unhygienic.
- Workload is heavy, due to which it demands heavy muscular work.
- Work and workplaces are not of permanent nature.
- Basic philosophy to improve their working conditions is the safety philosophy.
- Construction is inherently hazardous industry, contract base industry, demands heavy work load, contributes high frequency and severity of accidents, less protection by law, movable and needs continuous efforts to maintain safety at all levels.
- It may not be possible to completely eliminate the hazards, but it is certainly possible to minimize them by observing certain safety precautions in construction site.
- Thus improvement require to the working and service conditions of the workers for their Safety on Construction Site.
Major causes of Accident in Construction site:
- Falling from height.
- Struck by falling body including landslide, material and equipment.
- Striking against object.
- Falling on the flat or into pit, sump, gutter etc.
- Occupational diseases of lung, skin, and nervous system.
- Electrical and pneumatic tools.
- Unguarded machinery.
- Heavy vehicles movement.
- Working without safety equipments in construction site.
Although, Mechanization can eliminate some manual work hazard for safety on construction site.
Work permit system, prompt supervision and first-aid, use of personal protective equipment and proper tools, training and education and project safety committee are some of the remedial measures in construction site.
Parameters of Safety on Construction Site:
Studies, Statistics and Results:
A study by National Institute of Training for Industrial Engineering (NITIE), Bombay (1989) and after interviewing site engineers, safety officers and laborer on site, conclude that the reasons for health and safety problems were;
- The absence of safety rules and regulations in construction site.
- The unorganized nature of work.
- Generally total lack of any need for safety felt by engineers and contractors in construction site.
- Absence of trade unions for welfare, health and safety in construction site.
The main safety measures suggested in construction site were
- Compulsory use of safety helmets.
- Use of safety belts for working at heights greater than 1.8 m.
- Provision of canvas around the scaffolding to prevent falling objects from striking people.
- Good and tidy housekeeping.
- Provision of proper tools.
- Adequate training to new workers.
- Appointment of Safety officers in construction site.
- Record to maintain for that of recordable and non recordable accidents.
- Provision of qualified safety equipments in enough quantity in construction site.
The first major causes of fatal accidents due to lack of safety at construction sites are:
- Fall from height and
- Struck by falling objects.
Therefore safety work to eliminate these causes need first priority in construction site.
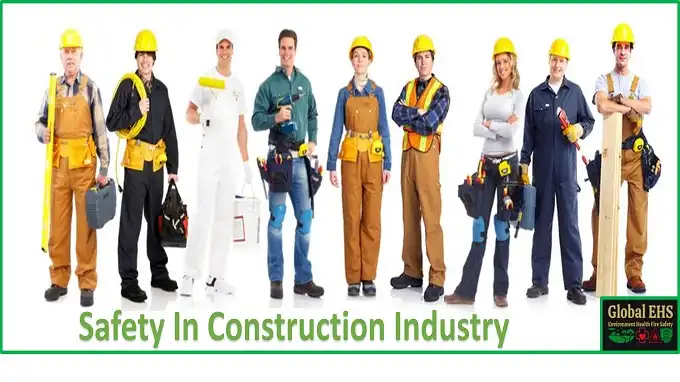
General safety statistics of nonfatal accidents of above mentioned in construction site gives following figures:
- Types of Accidents –
Fall from heights 15 to 22 %,
Struck by falling objects 13 to 33%,
Struck by others 21 to 38 %,
Electric shock 2 to 7%. - Agency / Activity –
Material handling 27 to 41 %,
Work at height 14 to 21 %,
Hand/Power tools 10 to 12%,
Fabrication & erection 12 to 13%. - Body parts injured –
Hand, Fingers & arms – 22 to 35 %,
Head & Scalp – 16 to 18 %,
Foot & toe 12 to 15 %,
Leg & thigh 9 to 17%.
Hazards at Construction:
Fall of Persons:
- Collapse of scaffold, Fall through opening, fall from height, structure failure, tripping.
- Fall from height may be due to non-use or failure of safety belt, lack of proper access, non-use of proper ladder etc. in construction site.
- Fall through opening may be due to unguarded opening or poor guarding.
- Collapse of scaffold may be due to its improper design, no toe board, no means of access. Minimum dimensions are: Board width 6”, thickness 1” and guard rail height 30 to 36”.
- Tripping may be due to loose object / cables etc.
Fire:
- Due to welding, gas cutting, smoking, gas cylinders, scattered wooden material / rubbish, paints/thinners, temporary shed etc.
Electrocution:
- Electric shock, burns, damaged cable, no earthing, no ELCB, no use of 3 pin plug/socket, work by non-qualified electrician etc.
Material Handling:
- No training, excessive weight lifting, improper or failure of lifting tackles, slings etc.
Transport Accidents:
- Untrained driver, due to not obeying traffic rules, reversing without signaling, over-speed, speed-breakers, poor brakes, poor lighting etc.
PPE:
- Due to not using helmet, safety shoes, hand gloves, safety belt, respirators etc. in construction site.
Others:
- Due to Noise, vibration, dust, gas, fumes, cave in, night work, overtime, intoxication etc.
Site Planning and Layout:
- In construction site, scope of site selection is less though not zero which is necessary to ensure safety.
- Mines are at permanent places though shifting is not possible.
- Builders or organizers generally purchase the site where land is available at low price and where contractors and workers have to work.
- In a permanent factory premises, carry out construction in a limited space.
- In dense population, construction of high rise (multi-storied) building due to which there is need working at height.
- Gutters and underground piping have fixed tracks available.
- Underwater work has fixed destinations and long pipelines passes through the shortest possible distance due to economic reasons.
- Therefore in a limited scope of site selection, planning and layout becomes most essential on the available site.
- Plant or factory premises vary in size and manpower employment.
- There are giant petrochemical and fertilizer plants on once end and small factory in a single room on the other end.
- As per legal requirement of more welfare facilities from bigger factories depending on number of workers and male-female employment.
- Stringent safety provisions are applicable to chemical plants and Major Accident Hazard (MAH) installations accordingly.
- There is requirement before starting a factory permission from local authority and other government departments.
- Where pollution is possible, permission from State/Central Environment department and Pollution Control Board is also necessary.
General Principals of Planning and Design:
- Good transportation facilities.
- Safe handling and storage facilities.
- Personal and welfare facilities.
- Engineering, utility and safety facilities.
- Walkway, stairs, platform, ramps etc.
- Good lighting and ventilation.
- Elevators and lifting machines.
- Boilers and pressure vessels.
- Fixed and portable machinery and equipment.
- Electrical installation.
- Fire protection.
- Other provisions for health and safety, viz. effluent disposal, water, firs-aid, emergency power, equipment and emergency planning etc. in construction site.
General principles of any workplace design:
They are as under;
- Plan the ideal, then the practical.
- Plan the whole, then the detail.
- Plan the work process and equipment around the system requirements.
- Plan the workplace layout around the process and equipment.
- Plan the final enclosure around the workplace layout.
- Use trails to evaluate alternatives and to check the final design.
Design aspects should include proper buildings and roads layout, storage & process layouts, proper heights, lights, depths, spacing and dimensions considering ergonomic requirements, loads and climatic factors and specific process hazards.
Some notable points for good planning and design are:
- Sound foundations,
- Stable construction and loading,
- Non-congested machinery layout (safety distance 1 m),
- No overcrowding (otherwise claustrophobia is possible),
- Minimum floor area per worker ( 1 to 2 m2), minimum alley width,
- Safe roadways, walkways, yards etc.
- Prescribed ventilation area (15% of floor area),
- Sufficient natural and mechanical ventilation,
- Humidity control,
- Sufficient natural and artificial lighting,
- Open plant for chemical processes,
- Dykes, boundaries and blast walls (to withstand 7 kgf/cm2 force),
- Safe layout and erection of chemical vessels and equipment,
- Ergonomic considerations,
- segregation of noisy and dusty processes,
- Fencing and covering of water-ways, reservoirs, ditches, floor opening, gutters etc.,
- Separate entrance and exit gates,
- Parking plots,
- safe layout of control room,
- provision of fire prevention and protection systems,
- Safe storage of flammable, explosive and toxic materials,
- Waste disposal arrangements for solid, liquid and gaseous wastes,
- Effluent treatment plant (ETP), scrubbers, incinerators, flare or exhaust as per requirement,
- Safe discharge of smoke, fumes, dusts, gases etc.,
- Maintenance of separation distances.
- Proper layout of utilities (water, power, steam, air, oil, inert gas etc.) and ancillary services,
- Safe transportation and security arrangement,
- Hazards identification and removal,
- Safe pipe work,
- Follow-up of standards, codes and reliability criteria,
- Limitation of inventory,
- Fail-safe design,
- Built-in safety devices etc.
Thus points of plant layout and design are numerous and selection of particular point depends on process, technical and safety requirements in construction site.
General Principals of Plant Layout
General Point:
- Size, shape, location, construction, buildings layout and other facilities should permit efficient utilization or machines, processes and materials. Decide need and possibility of one stored or multi-stored structure.
- Planning of Layout properly to allow smooth flow and efficient use of men, materials methods, processes, time cycles etc. and should allow good and safe working conditions for accident prevention or risk.
Some General Principles for good Layout are:
- Enough work Space (2 m2 per person) should be provided for workers to work without restriction.
- Proper roads, walkways, tracks, alleys, catwalk etc. should be provided for free passage of men and materials to avoid delay and obstruction.
- Sufficient doors, windows, ventilators and open space must be provided for good ventilation and lighting.
- Do Installation of machinery, floors, stairs, lifting machines, electric wiring etc, to ensure safety. Allow at least 1 m space around each machine.
- Keep the handling of materials to the minimum. Use mechanical means to reduce manual strain.
- Provide safe means of access to all work places.
- Provide safe transport facilities for men and materials.
- Provide adequate emergency exits.
- Purchase and arrange in orderly manner machines and equipment with built-in safely.
- Isolate high noise, vibration, fire, explosion and toxic hazards. Design a work bench, table, booth, roof, ladder, platform, sheet, support etc. with safety standards to avoid such hazards in construction site.
- Allow space for future expansion.
- Provide repair and maintenance workshop, welfare facilities and education and training facilities.
- Use appropriate colors, notices, signs, labels, posters etc. for safety.
- Provide easy locations of fire alarms, fire fighting equipment, personal protective equipment, emergency assembly points, medical Centre, safety office etc. in construction site.
- Provide and maintain good housekeeping.
Other factors of plant layout and design from safety point of view are:
- Safe design and construction using safety standards and good engineering practices.
- Statutory requirements for plant layout and design.
- Containment of leakage and accidents.
- Segregation of different risks.
- Safe storage, process, utilities and waste disposal design.
- Safe control room location & design.
- Emergency control devices.
- Fire fighting and gas leak control facilities.
- Ample water storage.
- Auto controls, alarms, trips, interlocks and necessary safety devices.
- Railings and guarding at chances of fall, cross over and on moving machinery.
- Roads of sufficient width and signs.
- Safe loading, unloading, transport and piping facilities.
- Security round the clock.
- Wind direction and speed indicator with recorder to know wind direction and speed.
- First aid Centre and ambulance van.
- Prepare the site layout is first, then the plot and equipment layouts. Sub-divide Site into blocks or plots. Equipment layout includes P & I diagrams and fire equipment layout.
- First, plan for the whole and then for the detail. Plan site layout, plot layout and equipment layout as per requirement. Prepare alternate layouts should for selecting the best one. Decide process flow diagram and stages or sequence of work. Subdivide each work in steps accounting for safety precautions and responsibilities.
- Properly plan facilities for water, fire fighting, first-aid, tools and equipment availability, roads, vehicle movement, parking, smoking booths, sanitary blocks, crèche, canteen, control room, safe entry, exit and escape route etc.
- All things considered Topography, geology, weather, environment, separation distances, service corridors, overhead work (pipe bridges, tanks, slabs etc), segregation etc.
- Encounter special precaution for working at heights or depths.
- Planning, layout and designing of steel structure, tall towers, metal tanks, vessels, reactors, utilities, piping etc. need Hazop, hazard identification, risk and reliability assessment, strength and stability criteria, inventory reduction, process safety, fail-safe design, emergency shut-down procedure and emergency planning.
- All things considered, appointment of safety and health personnel, trained supervisors and requirement of adequate first-aid and fire fighting facilities and personal protective equipment at the stage of planning and budgeting for safety at work.
Safe Access:
- For the safety of workplaces and avoiding risk of injury to workers, safe means of access to and egress from all workplaces should be provided, maintained and indicated whenever necessary in construction site.
- As per legal requirement all floors, steps, stairs, passages and gangways shall be of sound construction and maintain properly and keep it free from obstructions and substances likely to cause persons to slip and whenever it is necessary to ensure safety, steps, stairs, passages and gangways shall be provided with substantial handrails.
- Require safe means of access at all working places.
- Requirement to prevent fall, fencing or other devices.
- As per legal requirement, access for fire fighting and requires unobstructed layout of plants and building and doors and windows on external walls for easy access inside the building.
- Means of access may be a ladder-portable or fixed, ramp, runway or stairway.
- They should conform to the code or standards prescribed for the safety at construction site.
Safety Work Permit & Checklist:
- Follow a safety work permit (SWP) system is must for working at height, on scaffold, in confine space, in underground work, above ground work, in hazardous environment area etc.
Good Housekeeping:
Good Housekeeping programmes should include:
- Speedy removal of scrap, waste, debris, loose and unused materials at regular intervals.
- Proper storage of materials, tools and equipment. Removal of nails from lumber before stacking.
- Cleaning of floors, passageways, stairs etc. to remove oil, water, dust etc. Use of Sand, ash, sawdust and proper absorbers.
- Containers should be provided for collection and separation of waste. Cover Flammable / hazardous waste and dispose off safely.
- Lift excessive materials, tools and equipment and place in their proper places, After completion of any job.
- Piles of materials should be stable and properly supported.
- Avoid throwing of material. If there is no option other than throwing then give warning signals before performing and clear the area.
- Follow proper painting and colour-coding.
- At least at the beginning and at the end of a shift, supervisors should take round to check above points.
Construction Machinery
Construction machinery can be classified into three categories as under:
- Lifting Appliances and Gear:
Pulleys, chain pulley blocks, winches, hoists, derricks, gin poles, cranes (fixed and mobile), lifting ropes, slings etc. - Transport, Earth-moving and Material Handling Equipment:
Power shovels (excavators), bulldozers, scrapers, pavers, road rollers, pile drivers, mobile asphalt layers and finishers. - Plant machinery, Equipment and Handtools:
Concrete mixers and vibrators, pneumatic compressors, pneumatic tools, cartridge operated tools, electric tools, hand tools, conveyors, crusher plants, power generators, engines and silos.
Explanation of some salient safety features of these machines / equipment are as below:
Lifting Appliances and Gear:
Pulleys:
- Select the pulleys as per requirement.
- Don`t use Steel and nylon rope together.
- Grooves should be uniform and smooth and the rope (wire or fibre) should run free.
- Check Sheaves, shafts, hooks and pins (with locking) before use and Provide lubrication where necessary.
- Sheaves should rotate freely on the shaft.
- The shaft should be free from any defect or crack. Don`t use Worn shafts. Anchorage should be firm and strong.
- Use Anti-twister to prevent rubbing of the ropes with one another.
Chain Pulley Blocks:
- It should fulfill statutory requirements.
- Select the lifting capacity depending on the maximum load to lift.
- Verify its test certificate.
- Check for slipping of load, jamming of links and free operation.
- The chain should not come out of pulleys.
- It is better to lubricate before every use.
- Testing it periodically by a competent person.
- The anchorage should be strong and rigid.
- Check it for cracks, wear and tear, elongation etc.
- Don`t use Open out hooks and tamper block / puller.
- No cannibalizing on chain pulley blocks.
Winches:
- Mark Safe working load with gear arrangement on the winch stand.
- Place a winch on a firm base, anchor it properly and don`t overload.
- Check brake, ratchet arrangement, gear and pinion, meshing, wire rope and its clamping, rope drum and tie rod before every use.
- Adjust Tie rod to prevent clutch arrangement to slip.
- Keep ratchet arrangement in position while hoisting a load.
Hoists:
- Design should be as per standard code.
- Erect Outdoor hoist towers on firm foundation, brace it securely, guyed and anchored.
- Ladder way should extend from bottom to top.
- Enclose hoist shaft (way) with rigid panels or fencing at all landing platforms, access or whenever there is chances of any person is liable to struck by any moving part.
- The shaft enclosure, except at approaches, should be of 2 mt (minimum 1 mt) height above the floor or platform to prevent any person falling down the hoist way.
- Hoisting engine or motor should be capable of controlling the heaviest load.
- When the cage of platform reaches its highest point, make arrangement to stop it automatically (no overrun).
- Hoist platform or cage should be capable to carry the maximum load.
- It should have a safety gear to hold it if the rope breaks.
- At the ground floor coil springs should be provided to arrest any accidental fall.
- Cage or platform should have toe-boards or enclosure to prevent fall of material inside.
- Counterweights should run in guides. Interlock door should be provided whenever any worker has to enter the cage.
- Display notices of carrying capacity (weight/persons).
- Examination of factory hoists/lifts thoroughly examined by a competent person at least once in 6 months with report as per legal reqirement.
Derricks:
- They are of two types: Stiff-leg derricks and Guy derricks.
- Erection of Stiff-leg derricks on a firm base to withstand the weight of the crane structure and the maximum load. Prevent masts from lifting out of their seating.
- Don`t alter the jib length without consulting the manufacture.
- Arrange counterweights such a way that they do not subject the backstays, sleepers or pivots to excessive strain.
- Operate electrical derricks with proper earthing provision.
- In case of wheels-mounted derricks , maintain the correct wheel distance by a rigid member and provide struts to give support if a wheel brake fails or the derrick is derail.
- Provide support to the mast of guy derrick by six equi-distance top guys and the guy spread angle from the mast should be less than 45o from the horizontal.
- Ensure the restraint of the guy ropes by fitting stirrups or anchor plates in concrete foundations.
- Guy ropes should have a device to regulate tension.
- Lubricate pins and bearings frequently. When not in use, anchor the derrick boom to prevent it from swinging.
- Testing of the derrick by a competent person and do not overloaded.
- Check the mast, guyropes, wire ropes, swivel hook, rope clamps etc. before erecting the derrick. Check welded or bolted joints/parts for crack, defect and tightness.
Gin Poles:
They should be straight, made of sound metal of straight timber without knots, of sufficient strength and adequately guyed and anchored. Fasten them adequately at their feet to prevent displacement. Before their re-erection, inspect and test under load the pole, ropes, guys, blocks etc.
Cranes (Fixed & Mobile):
- Ascertain the crane capacity and check brakes before lifting a load. Park Mobile crane on hard soil and not near any pit or excavation.
- Safe working load of any crane depends on (a) condition of the ground (b) boom length (c) inclination of boom to the vertical (d) radius of rotation while lifting the load (e) out rigger blocked or free and (f) operator’s skill.
- Display the safe working load in the crane. Derate (lowered) it due to defects in welding, bend in angle, bracing and conditions of clutch, brake etc.
- Provide devices to prevent load movement to a point whenever the corresponding safe working load of the crane would the exceeded.
- Follow Standard signaling code, make it understand by the operator and train signalman. The crane operator shall respond to signals only from the appointed signaler, but shall obey a stop signal from anybody.
- Use tag lines while hoisting heavy and bulky load. Check the crane and its parts (brakes, boom, hook, wire ropes, pulleys etc.) regularly and maintain in good condition.
- The load should not touch the boom and the boom should not touch any live electric line or structure. Check quality of packing before lifting. Nobody should stand below the boom or load.
- The operator should be able to see the hook and the load, should keep his wind shield clean for clear vision and deck clean of any oil, mud or dust.
- When the hooks are at the lowest point, at least two dead coils should remain on the rope drum. Makeshift methods to increase the capacity of a crane are unsafe.
- During storm, anchor the hook block firmly and release swing lock. At the end of work, remove the load from the hook and raise the hook to the maximum height.
- The mobile crane should have horn, head light, side lamps, rear and stop lights and flashing direction indicators. Jib crane should keep the jib lowered while travelling without load.
- While travelling up a slope, Decrease the load radius and while travelling down, increase that radius. Constant watch on the radius is necessary while travelling on uneven surfaces.
Lifting Ropes, Slings, etc.:
- Safe working capacity of the lifting ropes must be known before hand.
- Install, Maintain and inspect ropes, slings, rings, shackles, tackles, chains, hooks, swivels etc. as per legal requirements.
- Don`t use repaired ropes in hoists.
- When there is use of multiple independent ropes to lift a load, ensure capability of each rope for carrying the load independently.
Transport, Earth-moving and Material Handling Equipment:
- All vehicles, earth-moving and material handling equipments should have following general provisions.
- They should be of good design, sound material and construction, adequate strength and maintained in good working order.
- Consider principles of safety and ergonomics in design and operation.
- Ensure operators / drivers training, medical & physical fitness and above 18 years of age. They should be competent, reliable and follow the signaling code. Take help of authorized signaler is must while driving backwards or there is restriction in view. Protect them against weather, dust, load and possible accidents.
- Equip all vehicles with proper lights, horns, silencers, power, hand brakes and reversing alarm.
- Check their motors, engines, brakes, gears, chassis, blades, tracks, wire ropes, sheaves, transmission parts and pneumatic, hydraulic systems daily before use.
- Do not left the vehicle or machine unattended with the engine running.
- Keep deck plates and steps free from oil, grease, mud etc.
- Keep the cab least 1 m away from a face being excavate.
- Do not use bucket excavators at the top or bottom of earth walls with a slope exceeding 60o.
- In case of caterpillar, Indicate gross laden weight, tare weight, maximum axle weight and ground pressure.
- When not in use, Place the boom in the direction of travel and scoop, And raise shovel or bucket without load.
- Safe parking place should be provided whenever more vehicles have to work.
- Do not allow anybody to rest or sleep under the vehicle.
Power Shovels (Excavators):
- Equip them with emergency stop device and two independent locking devices for brake pedals.
- The bucket teeth should not come nearer the boom than 40 cm.
- Display Safe working load of the lifting gear in the cabin and fit its indicator.
- Prevent the boom from swinging during transport.
- Do not pull the boom tight against the emergency stop while supporting a load.
- The wire ropes should be of specified diameter and construction.
- Do not exceed the safe operating radius.
- Operate the shovels such as not to loose their stability.
- The driver should see that no person is under or near the raised bucket or grab without doubt.
- When not in use, Keep the bucket resting on the stable ground and not hanging.
- Station the truck need to load at 60 cm. or more from the excavator even when it turns.
- Additionally, earthing and fire extinguisher should be provided where necessary.
Bulldozers:
- While moving uphill, Keep the blade low.
- Do not use the blade as brake except in emergency.
- Inspect the blade suspension arrangement, wire rope or hydraulic system weekly.
- At the close of work, Left the bulldozer on level ground and before leaving it, apply the brakes, lower the blade and ripper and put the shift lever in neutral.
Scrappers:
- Connect the tractor and scrappers by a safety line when in operation.
- Left Scrappers in gear while moving downhill.
- Prop Scrapper bowls when replacing blades.
Pavers:
- Guards should be provided to prevent workers from walking under the skip.
Road Rollers:
- Check the land for bearing capacity and general safety before using a road roller in construction site.
- While moving downhill the engine should be in gear.
- When it is not in use, Apply the brakes, Block the wheels, switch off the contact and make engine in bottom gear if the roller is facing uphill and in reverse gear if it is facing downhill.
Pile-drivers:
- All pile-driving equipment should be of good design and construction and properly maintained.
- Take Ergonomic principles consideration.
- Carry out Pile-driving under the supervision of a competent person only.
- Underground services should be located and rendered safe before starting piling.
- Support Pile drivers firmly on sound foundation. If necessary, guy them too.
- If two pile-drivers have to work nearby, separate them by a distance at least equal to the longest leg.
- Make Electrical conductors dead, If they are in proximity.
- When leads have to incline, counterbalance them and secure tilting device against slipping.
- Securely lash the hoses of steam and air hammers to the hammer so as to prevent them from whipping if a connection breaks.
- Prevent overturning of a pile-driver.
- Prevent out coming of the rope from the top pulley or wheel and missing of hammer from the pile.
- Inspect Pile lines and pulley blocks before the beginning of each shift.
- Employ only trained operators regardless.
- Use of suitable signals, ear protectors and safety helmet specifically.
- Prepare piles at a distance at least equal to twice the length of the longest pile from the pile-driver.
- When not in use, Block the hammer at the bottom of the leads.
- When pile-drivers are working over water, Keep a suitable boat readily available at all times.
- Provide whistle, siren, signals, fire fighting equipment and sufficient sheaves, distribute the weight of machinery and provide water-tight compartments with siphons to remove water seepage particularly.
Mobile Asphalt Layers and Finishers:
- The mixer elevator should be within a metal enclosure with a window for observation, lubrication and maintenance undeniably.
- Bitumen scoops should have covers.
- The sprayer should have fire resistant shield with an observation window.
- Non-foaming products are preferable. Reflective jackets should be provided to workers working on public roads.
- The fire extinguishers are necessary near spreader and others in readiness accordingly.
- Do not use naked flame to see the level of asphalt in the tank.
- Do not heat Thinners on open flame in any case.
- Do not allow inspection doors in open condition in any case if there is any pressure in the boiler.
- If there is extinguishing of burner flame, cut the fuel supply and blow the heating tube thoroughly out by the fan to prevent backfire.
Plant Machinery, Equipment and Hand tools:
- All such machinery, equipment and tools should be of good, ergonomic and safe design, maintained in good working order and operated by trained operators with necessary personal protective equipment accordingly.
- Follow safety instructions from manufacturer and safe operating procedure in construction site without any doubt.
- Power driven equipment should be properly earthed, stop switch provided in close proximity, adequately guarded, speed regulated and when not in use, switched off (de-energized) and isolated before any major adjustment.
Concrete Mixtures:
- Ensure guarding and fencing of all gears, chains, rollers and open revolving blades.
- Protect hopper by side railing to prevent workers from passing under the skip accordingly.
- Check hopper hoisting wire rope, brake, skip hoist clutch and blocking (fixing when raised) device and adjust it regularly.
- Double earthing and insulation of electrical part is necessary.
- Before allowing a person to enter the drum for cleaning or repair, remove electrical connections (fuses).
- Erection of concrete bucket towers and masts with pouring gutters or conveyor belts by competent persons and inspect it on daily basis.
- The winch operator should be able to see the filling, emptying and lowering of bucket, otherwise a banks-man should direct the operator.
- Align guides for bucket correctly to prevent the bucket from jamming in the tower.
- Structure or scaffold carrying a pipe for pumped concrete should be strong enough (factor of safety 4 or more) to support a filled pipe and all workers on it. Securely anchor Such concrete carrying pipes at the ends and at curves, provided at top with air release valves and securely attached to the pump nozzle.
Concrete Vibrators:
- Completely enclose vibrating unit and ensure belt guarding.
- Protect electrical vibrator by overload relays and earthing.
- Cable length should be sufficient.
- Lock needle load firmly.
- Lubricate needle inner core.
Pneumatic Compressors:
- Testing by a competent person is necessary.
- Equip air receivers with a safety valve, pressure gauge, drain cock and openings for inspection and cleaning.
- It is safer to provide a PRV, a stop valve and an oil separator between the air receiver and the compressor.
- Equip compressors with an automatic device to control the safe discharge pressure, a quick release valve and suitable arrangements to prevent or remove contamination in a confined space.
- Whenever there is chances of explosive gas mixture formation in compressor, protect it against sparking.
- Ensure water flow in water-cooling jackets.
- Inter and after coolers should be able to withstand the maximum pressure in the air discharge piping. Such piping should be provided with a fusible plug and insulation to protect workers against burns and fire risks.
- Whenever there is installation of stop valves in air-discharge piping, ensure easy accessibility for inspection and cleaning and Install one or more safety valves between the compressor and the stop valve.
Pneumatic Tools:
- Place operating triggers on portable pneumatic tools such as to minimize the risk of accidental starting of the machine and so arranged as to close the air inlet valve automatically when the pressure of the operator’s hand is removed.
- Equip air hoses and their connections with safety clips or retainers to prevent dies and tools from being expel accidentally from the barrel.
- Before any adjustment or repair, disconnect power and release pressure in hose lines.
Cartridge-operated Tools:
- Use preferable low-velocity tool. Provide such tools with a cover(guard) which will not open without rendering the tool inoperative, devices to prevent from accidental firing, to prevent firing if the muzzle is not press and to prevent firing if it is not perpendicular to the working surface.
- The recoil should not be capable of injuring the user.
- Inspect the tool for all safety devices and to ensure un-obstruction of the barrel.
- Do not store or operate cartridge-operated tool should in explosive atmosphere.
- When not in use, Keep it in its special container for the purpose of safety.
Electric Tools:
- Operate portable electrical tools at low voltage and with ELCB to avoid risk of shock.
- Provide proper earthing with metallic cases.
- Provide earthing to all insulated or double insulated tools.
- Carry out periodic inspection and maintenance by a competent electrician.
- Proper fuse and insulated handle are necessary.
Hand Tools:
- Allow only competent person to temper, dress or repair hand tools.
- Keep cutting edges sharp.
- Dress or ground heads of hammers and other shock tools as soon as they begin to mushroom or crack.
- When not in use or while carrying or transporting, keep them in suitable containers.
- Use only Insulated or non-conducting tools near live electrical installations.
- Use Non-sparking tools only near flammable vapors.
Conveyors:
- Ensure Smooth running of conveyors.
- Ensure guarding of nip between tight belt and pulley/roller and other transmission parts. Provide bridge with hand railing, If they are not entirely enclose. Emergency stop-devices (e.g. cord of cable) should be easily accessible.
- Stop buttons should be provided at drive and take-up ends.
- Where two or more conveyors operate together, arrange control devices such as that no conveyor can feed on to a stopped conveyor.
- When a conveyor is discharging into a bunker or hopper, the feeding conveyor should be provided with an overload switch.
- Also cover screw conveyors always.
- Do not open cover without stopping the conveyor in any case.
Crusher Plants:
- They should be located away from construction area to keep away dust, sand, gravel, noise and vibrations.
- Extra isolation switch should be provided to prevent accidental starting during repair or maintenance.
- Electrical motors, switches and instrumentation should be dust and moisture proof.
- Clean access roads to the crusher hopper and screens by water spraying.
- Lay power cables underground or at safe elevation.
- It is equally important to clean all equipment, plant and machinery of dust and sand daily.
Power Generators:
- House them in a concrete room or insulated area to minimize noise effects accordingly.
- Silences and exhaust pipes should be provided.
- Extra isolation switch should be provided to avoid accidental starting during maintenance.
Engines:
- Do not exceed maximum safe speed.
- Provision of remote control device to stop or limit the speed accordingly.
- For internal combustion provide engines, exhaust ventilation and while fueling, avoid spark and keep fire extinguisher ready.
- Secondary fuel tank should be provided outside the engine room.
Silos:
- Erect silos on sound foundation and capable of withstanding stresses without any deformation of walls, floors and other load-bearing parts.
- Safe means of access (stairs, fixed ladders or hoists), quantity/ level indicator, notices, blockage remover and fire extinguishers should be provided.
- In silos where explosive mixtures are possible, flameproof all electrical equipment and hand lamps, use non-sparking tools and provide explosion vents in the walls at safer points accordingly.
- Before allowing workers in a silo, make work permit should, close charge (filling) opening and provide safety belt with lifeline in the hands of another person outside if they have to work on loose material.
Underground Works
- Underground work includes excavations in surface soil or rock, drilling, blasting, trenching, shoring, strutting, tunneling, piling, shaft sinking, haulage and underground pipelines.
- It requires due considerations of underground lighting, ventilation, electricity, dust control inrush of water, oil or gas and continuous safety of people at work.
Some explanations of provisions are as below:
- As per legal requirements for excavation and tunneling works including warning signs and notices, illumination, stability of structure, pilling, shoring and bracing, safe access, trenches, tunneling operation, shafts, pneumatic tools, inflammable oils, coupling and hoses, storing of oil and fuel underground, use of gases underground, water for fire fighting, flooding, steel curtains, exposure limits of chemicals, ventilation, air locks, man-locks, medical lock, emergency generators etc.
Excavation:
- Requirement of foundation or underground support for most of the constructions and method of reaching earth or rock stratum suitable for foundation is excavation.
- It may be with or without dewatering the site and out of many methods select a suitable method of excavation.
- General precautions for any excavation or underground work are: survey of hazards of fall of persons, soil, material etc., inrush of water, oil, gas etc., adequate lighting and ventilation to supply fresh air inside, controlling gas, vapor, dust etc. within safe limits, fire precaution, safe means of access, stability of the ground, position of public utility services such as electric or telephone cables, water, gas or sewers line etc., effect on adjoining building, structure, roadways, bridges etc. A competent person should make this survey and give permission to work.
- If necessary, isolation of underground utility services should be effected by due permission or otherwise be protected.
- It is equally important to remove chemical waste and contamination safely.
- Do not move load, vehicle or material or stack near the edge of excavation unless shoring or pilling is requires to prevent the sides from collapsing.
- Regularly check all support work such as props, wedges etc. for deflection or distortion.
- Provide fencing by barrier to all sides at least up to 1 m and provide a danger notice and red signal and light.
- Slope is must to sides of all excavation to a safe angle not steeper than the angle of repose of a particular soil.
- Do cutting from top to bottom.
- Do not allow undercutting of side.
- In narrow trenches extend a ladder from bottom to top and 1 m above the ground surface.
- Prevent erosion of soil over excavated pits, trenches etc. from running water by dewatering pumps etc.
- Provide road-barrier at a distance if need to block road.
- Provide helmets and gum-boots to all workers working inside.
- In large scale excavations for dams, huge buildings, highways, railways etc., accidents occur mostly due to the vehicles, dumpers, trucks etc. Therefore must check such vehicles for warning sirens, horns, lights, signals, reverse alarm etc. Enforce rules of driving. Sufficient lighting should be provided for night work.
Drilling, Loading and Blasting:
- Requires drilling and loading before blasting.
- Before starting drilling, Check for any presence of unfired explosives carefully.
- Do not allow drilling in the butts of old holes.
- Before drilling, Remove loose or disintegrated rock by hand tools or pneumatic jack hammers to protect drillers against falls of material. Whenever this is not possible, a protective canopy or overhead screen should be provided.
- Drill holes by pneumatic hand-hold drills to a specific pattern. Compressed air hoses should have self locking couplings. Drillers should wear helmet, hand gloves and gumboots.
- After checking the drilling pattern and depth, Withdraw the drilling crew from the site with all drilling equipment and accessories.
- The blasting foreman will check all the holes needs to load by explosives and detonators for blasting.
- Govern transportation, storage, handling and use of explosives by the Explosives Act and Rules.
- Do not allow smoking or open flame in explosive loading area.
- Withdraw all the workers from this area to a safe place.
- Use only suitable battery lamps during loading shot holes.
- Do not load holes except those which needs to fire in the next round of blasting. Holes loaded during one shift should be at least 3 mm more than the dia of the cartridge.
- To avoid misfire, the detonator should be completely inserted length-wise in the cartridge and fastened in such a manner that it cannot be pulled out accidentally.
- Do not force the cartridges into the holes.
- Cap crimpers of proper design should be used for crimping the blasting caps into fuse. A knife or teeth shall not be used for this purpose. Intensity of charge to be loaded must be well calculated and safe enough to prevent damage to nearby structures due to shock and vibration resulting from explosion.
- Do tamping of cartridge in the hole by a wooden (or non-sparking metallic) stick gently. In case of removal of dynamite from cartridge, do not tamp loose dynamite. Never tamp primer. During tamping excise care to avoid injury to fuse or cap wires. Fill the holes with clay and sand sticks at the top. Ensure detonators’ wires is not in damage or pull out condition.
- Then check the continuity of the entire circuit by a blasting circuit tester and the resistance of the circuit is also measures. Do not allow other electric circuit should in that area or de energize it. Radio, TV and Radar transmitters can detonate electric cap. Hence maintain minimum safe distance.
- The lead wires are connected to the exploder whose firing switches are kept ‘open’ locked and keys with the blasting foreman. Return The surplus explosives/detonators to the magazines.
- Then follows the warning procedure. Establish ‘Warning’ and ‘All clear’ signals and ensure known to all concern. Trained persons are posted at all approached with red flags to stop all traffic and by passers.
- The blasting foreman, then, sounds warning siren to drive away all persons from the danger area and not to allow anybody to enter in the blasting area. After satisfaction with the readiness of blasting, the blasting foreman will fire the shots by closing the switch of the exploder. After dispersion of gases and dusts, the foreman will return to the area and check for any misfire.
- Misfire can be minimized by using good quality explosives, testing each electric cap with a blasting galvanometer before loading or by testing the complete circuit before firing.
- The safest way to deal with misfire is to re shoot it by new primer. If there is no misfire, then he gives ‘All Clear’ signal and allows the removal of blasted materials. Scale down loose rock.
- Carry out haulage i.e. pulling and shifting of material after blasting manually or mechanically. Ensure working head-lights, tail-lights and loud horns of vehicles (train or trucks). Do hauling by winch under the supervision of a competent person. Do not allow transport of workers along with the material.
- Maintain blasting record. Record date and time of blast, number of holes, type of explosives and detonator used, amount of charge per hole, firing pattern and sequence.
Shoring and Underpinning:
- They are required to stop settlement of a weak foundation, to strengthen the foundation to carry added loads, to provide support because of adjacent operations and to prevent deterioration of the foundation materials.
- Shoring refers to removal of temporary supports after completion of job and underpinning refers to providing permanent supports which remaining place even after completion of job.
- Shoring requires skilled workers and cordoning off the area due to hazardous nature of the job. Carry out it under constant supervision and control of qualified and experienced engineer. The jack, needles and temporary supports should be of adequate capacity and strength to raise the structure.
- Types of shores available are raking, flying, needle beam and post. The shores and needles to be underpinned must be designed to withstand the anticipated load.
- Underpinning is useful to stop settlement of the structure, or to give more support by new foundations to withstand added load of the structure. Do this work rapidly, in a limited space and with great care, to the existing structure.
- Adequate lateral bracing helps obviate the need of underpinning interior walls or columns.
- If damage results during underpinning and repairs required, it is best to wait till all settlement and lateral movement are ceased.
- Generally two methods are available for underpinning – the pit method and the steel cylinder or caisson method. The pit method is used whenever new foundation is not to be very deep. In the other method, the steel cylinders of caissons are placed under the existing footings and sunk to the rock. Skilled workers are required due to restricted availability of working space and headroom. The shoring of the column is removed at the end.
Tunneling and Shaft Sinking:
- Tunnels are required for road-ways and railways through mountain, hydro-power station underground, irrigation of water, drainage, mining of minerals, storage of hazardous wastes and defense installations (underground shelter) etc.
- Tunneling may be in soft ground (clay, sand, gravel or soft earth) or in rock. Soft ground tunneling is carried out by fore poling, needle-beam and timber, liner plates, shied and liner plates and plenum process or compressed air-lock. Rock tunneling is carried out by drilling, blasting, mucking or by machines which may be full face boring machine or the header with rotary milling head on a telescopic boom.
- Safety measures include well maintained equipment and tools, their testing by competent persons, speedy removal of debris, refuse and trash, safe and adequate walkway, proper drainage and water pumping if required, good lighting, use of helmet, gumboots, and goggles by the workers, jumbo platform with guard rails and toe-guards to work near the entire face of the tunnel to be drilled, pneumatic drills with pusher legs, wet drilling for dust control, pneumatic coupling with self locking couplings, separate transport vehicles for explosives and detonators and their separate magazines, safe handling of explosives and detonators, avoidance of spark, no smoking in explosive area and all precautions for drilling, loading, blasting and haulage.
- After blasting, rock falls can cause major accidents.
- Therefore inspection of walls and roofs, scaling of loose rock, bolting and supporting of weak sports, checking of weak seams and planes by a hand hammer and supporting of roof and sides are essential.
- Mechanical loading of muck and haulage are required for speedy construction in tunnel.
- Muck (dirty thing) cars should be loaded evenly and not piled above the sides.
- Vehicles in tunnel should not run overloading and over speeding.
- Rail – tracks should be safe and sound. Smokeless locomotives should be used.
- Dump cars should be with locking device to prevent accidental tipping.
- When tunneling is done through a shaft (vertical rod or stem), the tunnel musk is hoisted through the shaft and brought to surface for disposal.
- Hoisting machines should have automatic brakes to stop and hold the conveyance (cage or car) if the hoisting power fails. It should have a depth indicator.
- Rules for hoist/lift should be followed.
- Mechanical ventilation is necessary in all tunneling work to supply fresh air to the working crew and removal of dust, fumes and gases including methane, CO2, etc. Rock dust containing silica and quartz may cause silicosis. Ventilation ducts should be airtight and should have reversible duct blowers to operate in both directions.
- The tunnels are lined with plain or reinforced concrete or steel forms to support the surfaces and to prevent any rock fall. Scaffolding carrying pipeline of pumped concrete should be strong enough.
- The workers should wear face shield or safety goggles in construction site.
- Safety precautions for shaft sinking are mostly same as stated above. The shaft which is not sunk through solid rock should be cased, lined or otherwise made safe. Workers should be provided with cradles from which they can work safely. The shaft top should be protected by fencing or guard-rails, toe-boards and gates. Means of escape and ladder from bottom to top should be provided in addition to any mechanical means of ingress and egress. Winches at shaft tops should provide easy replacement of bucket. All landings in shaft should have gates that close the opening to a height of at least 2 mt.
- All shafts of over 30 mt in depth should have an adequate head frame strong enough to withstand the maximum load. It should be open steel work, fire-resistant and protected against lightening.
- Shafts should have a signaling system that warns the hoisting man when a conveyance passes beyond the safe limit of travel. The signal code should be posted in the hoisting machine room and at each landing.
- No combustible material or structure should be allowed within a shaft, tunnel mouth, engine house or fan house.
- Lubricating oils, grease and rope dressings should be kept in closed metal containers and away from shafts.
- Electrical installations in shafts and tunnels should comply with rules and regulations.
- Lightening arresters should be provided on the surface.
- Provide emergency lighting to function for a long time (to escape safely) in construction site.
Above ground works
- Most of the construction works in the form of concrete, steel, wood or mixed structure are found just on the ground. Basic requirements to work at height as the work proceeds, are scaffolding, ladders, staircases, centering, formwork, wall and floor openings, structural steel work and machinery and equipment for the movement of material and men.
Structural Frames, Formwork and Concrete Work
- All such works require trained workers and the supervision of qualified and experienced engineer.
- Temporary work (framework, slip enough to withstand loads on it and working platforms, ladders, bracing etc. can be attached to it.
- Safety of workers from temporary, unstable or weak structure has to be foreseen in construction site.
Erection and Dismantling of Steel and Prefabricated Structures
- Safety of workers should be ensured by providing sound scaffolds, platforms, ladders, gangways, boatswain’s chairs, belts, fall arrester nets and lifting appliances including power driven mobile working platforms.
- All such platforms must have safety railing (at least 1 m high), hand rails and toe-boards in construction site.
- Free end of the safety belt must be tied with a fixed and strong support.
- Helmets, goggles, gloves, aprons and other equipment should be worn by the workers in construction site.
- Floors, stairs and platforms should be dry, clean and non-slippery. This can save many injuries.
- Hooks for lifting and transporting prefabricated parts or material should be of self-closing type and withstand load and stresses. Precast concrete parts should be allowed to set and harden for its full strength.
- Stores and racks of steel and so arranged as no part should fall or overturn.
- Lifting appliance should be suitable and tested at 20% more load. Tongs, clamps etc. should be capable of securing grip and marked with maximum permissible load.
- Lifted structure and wall units should be so placed that they do not fall by wind, jerk or other factors.
- Adequate instructions should be given to the workers for safe erection. If due to high wind, rain, snow or reduced visibility, it becomes unsafe to work, the work should be interrupted. Parts to be erected at a greater height should be assembled on the ground.
- While lifting prefabricated parts, area underneath it should be barricaded. Steel trusses being erected, should be firmly shored, braced or guyed until they are permanently secured in position and no workers should be allowed to work under them at that time.
- A boom or any moving part of a crane (including the load lifted) should not touch such trusses. In absence of such precautions, six workers died in one accident when trusses fell down on workers working underneath.
- No load-bearing structural member should be weakened by cutting, drilling etc. Open-web steel joints should be directly placed in position and secured against dislodgement.
Cast-in-situ Concrete Structures:
- The planning of construction of cast-in-situ, large span and multi-story concrete structures should provide information on specifications of materials to be used, methods of safe placing and handling, reinforcement design and load-bearing calculations.
- During construction, a daily progress report should be maintained, stage-wise erection procedure should be prescribed, defects watched continuously and loads should not be dumped or placed on setting concrete.
Wall and Floor Openings:
- Walls should be on sound footing, perfectly vertical, properly joined and of sufficient thickness of strength and load-bearing. Brick joints should be properly aligned, cemented and pointed if required. Plastering and colour coating give extra protection. Support of the wall under construction should not be taken but a scaffold should be used. Doors, windows, ventilators and other openings in walls should be provided as per requirement and drawing. As per Rule 18A, GFR, they should begin within 1 m from the floor.
- Floor construction uses a variety of material depending on choice. Earth filling with cement or cement concrete is necessary for strength. Wooden planks, steel grate (grill) or plates, tiles, stones, marble, cement concrete, asphalt etc. are some of the flooring materials.
- Floor openings are required for erection of hoist or lift way, tank, vessel or reactor, piping etc. Till these floor-gaps are not occupied by their proper fittings, they pose danger of falling from height. Therefore Section 33 of the Factories Act requires that all such floor openings should be securely covered or fenced. If any gate is provided at any landing platform, it is to be kept locked (not simply closed and openable) when any person has to work near it. In absence of such unlocked gate, a worker fell from a 30 m height and died on the spot.
Formwork and Slip forms:
- Tabular steel frames used as staging to support concrete form-work should have a safety factor of at least 2 and be used as per manufacturer’s recommendation in construction site.
- Struts and / or diagonal braces must be in proper position and secured for frames to develop full load carrying capacity.
- As erection progresses, all connecting devices should be in place and fastened for full stability of joints and nuts.
- As height increases above two tires, suitable planking should be used as a working platform. During concrete pouring operation, staging system should be constantly watched and corrected if necessary.
- Prepare concise procedures to cover all stages of work and supervise it by a competent person.
- Check foundations for ground conditions.
- Explain drawing or sketch for shuttering to workers.
- Shoring should be provided for support and should not be removed until authorization and the concrete has acquired sufficient strength.
- Shoring should be braced or tied together to prevent deformation or displacement.
- Mechanical, hydraulic, pneumatic or vacuum lifting devices should have automatic holding device in case of power failure.
- Workers placing, reinforcement rods and unloading concrete above the slipform platform should wear safety belts and lanyards to protect from falling in construction site.
- Slipform floor whenever reinforcement rods are being lifted should have temporary barricades.
- While lapping/joining vertical reinforcement roads, the projections should be tied to prevent their failing off inadvertently.
Structural Steel Work and Erection in construction site:
- A fabrication yard should well away from a rail-track, overhead transmission lines, boiler house and source of ignition.
- While unloading structural steel wagons or trucks by crane, wheels should be made stationary by fixing wedges and nobody should stand under a hanging load.
- While putting heavy structure, give proper supports (props) to prevent toppling.
- At both ends of a gantry crane, stoppers should be provided.
- Use of leather gloves, goggles etc. as per requirement.
- Portable tools should have guards, proper fuse, earthing and ELCB in power connection.
- In erection work load should be ascertained for Centre of gravity and its transfer at the slinging point.
- Lifting machines, ropes, slings, tackles etc. should be checked for its good working order and safety in construction sites.
- Eye bolts should be provided at correct slinging points while lifting heavy machinery such as motors, turbines, generators etc.
- Do not overload sling.
- Signaling code should be known to all. Use proper tag line for guiding while lifting loads.
- Stack of structural members should be such that light members should be at the top and in sequence of erection and not in a position to roll down or slide while handling.
- Allow clear passages.
- Hands should not be jammed against any object.
- Keep bolts, nuts, tools etc. in boxes and not loose on the structure.
- Ties vertical column by 4 guy ropes and only after bracing or fixing, remove the ropes one by one. Lift CI/GI sheet manually by proper system. It should not full. Keep them tied on top and bolted or stitched ultimately.
Underwater Works
- Work under or over water, there is requirement for deep foundation, well sinking, river dredging, underwater pipelines, tunneling, concreting, cofferdam, floating structure an special operations pertaining to irrigation and marine purposes to fulfill.
General Provisions for safety in construction site:
- Main safety measures at construction site necessary are
(1) to prevent workers from falling into water
(2) to rescue them in the event of drowning and
(3) safe and sufficient transport and life saving equipment in construction site. - Life buoys, life jackets, manned boats, fencing, safety nets, safety harness and protection from reptiles and other animals are also necessary in construction site.
- Bridges, footbridges, pontoons, walkways, gangways and workplaces should posses sufficient buoyancy, strength and stability be wide enough to allow safe movement of workers, free from nails, bolts, knots and tripping hazards, boarded over, lighted sufficiently, be provided with life saving equipment, toe-boards, guard-rails, hand ropes etc., be kept clear to tackle, tools and other obstructions, be made non-slippery by spraying sand, ashes etc, be anchored to prevent run away, be provided with ladders with safety hoops.
- Floating structures should have shelters, lifelines, gaffs, ring buoys. Rafts (logs), if used, should be strong enough to carry loads, securely moored and have safe means of access.
- Iron decks should be studded with non-slip surface and deck openings should be fenced. Floating pipelines should have safe walkway. No person should enter a hydraulic dredge gear room without informing the leverman and without being accompanied by a second person. Inspect hoist lines, drag lines, buckets, cutter heads and bridles on daily basis. Embark and disembark workers only at safe suitable landing places and counted regularly.
Boats:
- Boat used to transport workers by water should comply with legal requirements if any. It should be manned by an adequate and experienced crew and be equipped with life-saving appliances.
- The number of persons that can be transported safely should be marked as clearly visible and no more person than that must be allowed.
- Tow-boats should have a device to quick-release extinguishers. Tow-boats should carry a spare set of oars.
- Construct rescue board properly and of sufficient length and beam to afford stability.
- For work in tidal waters or fast flowing rivers a power driven craft should be provided with a fixed self-starting device on the motor. When not patrolling, Run their engines several times a day to ensure full efficiency.
Rescue and Emergency Procedures:
- Buoyancy-aid like life-jackets should be provided to rescue crew. Operatives should not work alone and provide training for emergency procedures.
- As per legal requirement, requires emergency action plan to handle emergencies like drowning of workers, sinking of vessels, fire and explosion, shed, structure etc., gas leakage, spillage of dangerous goods, land slide, floods, storms etc. It should be approved by the Director General.
Well-Sinking:
- Shaft-sinking operation for digging well or tunnel pose various hazards like wet and slippery footing, cramped working space, insufficient lighting, unknown weakness in rock or soil, handling of explosives and detonators, hoisting and haulage of muck and accidents due to machinery and mistakes in working methods. Dewatering pumps, shoring machine guarding and control devices, use of personal protective equipment, training and supervision are useful remedial measures.
Cofferdam:
- Underwater excavation is carried out by (1) Pumping out the water if inflow is not excessive (2) Isolating the site by a cofferdam (temporary bund) (3) Sinking caisson (box) with or without compressed air or (4) Chemical consolidation.
- The cofferdam is a temporary structure to exclude water from water-logged soil, river or the sea to enable the excavation and carry out construction in the dry. We can make the cofferdam out of earth, concrete, sheet piles or sheet cell.
- The earthen cofferdam is possible in shallow water with low velocity of current. Construct the earthen bank 1 m of the top water level. Due to water seeping and leaking such dam can fail. Therefore constant watch is necessary.
- We can construct sheet piled cofferdam by using a floating structure with machinery and crew. Only allow trained members in floating pile-driving crew to handle boats. Place the interlocking sheet piles and bracing in a cellular form through water. Vent fuel tanks below deck of the floating pile-driving equipment to the outside air with flame arresters. Workers handling piles should wear leather gloves. A competent person should constantly supervise.
- After erecting the cofferdam, pump out inside water. Do the excavation in dry soil up to a sound strata, lay down the foundation and build the structure. Dismantle the cofferdam thereafter.
Caissons:
- Use a caisson type structure as a part of foundation. Unlike cofferdam, it is a permanent structure and forms an integral part of the bridge or building foundation.
- The caissons are of three type
(1) A box caisson which is in closed position at the bottom but open at top to the atmosphere
(2) An open caisson which is open at both the ends and
(3) A pneumatic caisson which has a working chamber with roof in which air pressure is in maintained condition to prevent the entry of water and soil into excavation. - The box caisson is possible whenever no much requirement of excavation under water. The box is prepared of concrete or stone masonry on a dry dock, floated out to the location of sinking, sunk at the place of foundation bed and filled with mass of concrete or sand.
- The open caisson is a hollow cylinder or rectangular hollow shaft made of timber, masonry or RCC. Its bottom edge is V-shaped (pointed) and known as cutting edge. On reaching foundation level, place mass concrete to plug the cell after which requires to pump any water out and further place concrete to form the final seal. Such open caisson is possible on soft soil and not suitable on hard or irregular rock surface.
- Whenever piles driving or open caisson is not possible, create the pneumatic caisson by compressed air to drive water out of the working space for men and voids in material which need to excavate and thereby making the inside dry for easy working. Supply more than 1 m3 or 285 liters of fresh air per minute per person in the chamber at a pressure below 2.5 bar. During compression keep initial pressure is about 0.25 bar until confirmation that no person is feeling discomfort, and thereafter raise it at a rate not exceeding about 0.5 bar/min. Standby power should be available to the air compressors.
- To improve the working condition and to reduce the incidence of caisson sickness, the air should be warned in cold weather and cooled in hot weather. In tropical climate, it should be dehumidified to keep the wet bulb temperature below 25o C. in air and water tight chamber, openings for men and materials are provided at top in the vertical shafts with air-locks. The shafts (and openings) extend from the roof the caisson to a level well above the water level outside. The man-lock should be of sufficient size and equipped with pressure gauges, communication system and man-lock attendant.
- Every caisson, shaft, working chamber, medical lock and man lock should have a minimum internal height of 1.8 m. The door between the working chamber and the man lock leading to a lower pressure should be kept open when any person is working inside and the lock is not in use. Air supplied to the caisson from a compressor should be clean and non-polluted. All air lines should be in duplicate and with non-return valves to prevent the air escape from the chamber if pressure in the line fails. There should be a standby compressor for emergencies and two separate power supplies for each compressor. There should be two independent sources of electrical supply for lighting. Exhaust valves should be provided on chamber for clearing the air when necessary.
- Maintain reliable means of communication such bells, whistles, telephones etc. at all times between the working chamber and surface installations. Provide an adjustable safety valve on the outside of the bulkhead to a separate pipe leading from the working chamber through the bulkhead to the outside air.
- Every caisson and shaft containing flammable material should have water lines, hose connections and fire extinguishers.
- In all tunnels 5 m or over in diameter or height, a well-guarded overhead gangway should be provided from the working surface to the nearest airlock with an overhead clearance of at least 1.8m.
- Effects of air pressure on human body may be light (known as bends) or severe resulting in paralysis or death.
- Pain in ears, stomach and joints (like rheumatism), profuse cold perspiration, dizziness, giddiness, double vision, incoherence of speech, heat and feeling of resistance to move owing to density and pressure of air are reported.
- Rapid lowering of air pressure (decompression) cause severe effect as the nitrogen comes out from the body fluid (mostly blood). Therefore must ensure carry out slow depressurization.
- Ensure physical fitness of the workers (not fat, and with normal lungs, kidneys and good heart rate), above the age of 20 and ensure medical re-examination at least every 2 months or earlier. Keep a first-aid box in the working chamber.
- To counteract the effect of cold, the air-lock should be warmed, the men coming out (emerging) should be given hot drink and they should dress warmly. The best cure for ‘caisson disease’ is recompression with slow decompression. Achieve it by putting the patient in a medical air-lock for this purpose. Employ this trained lock keepers and medical lock attendants in the works. The medical lock should have two compartments so that it can be entered under pressure.
Demolition
- Demolition of very old, life-ended, weak or unsafe construction becomes necessary. Sometimes there is requirement for a new construction, alteration, addition or repairs on the same site. Involvement of high risk is due to falling or flying material, working at height or on a broken structure, use of heavy hand tools and heavy blows and vibration or sudden collapse. Ensure protection not only the workers but the public passing by Proper planning, permit, procedure, sequence of work, training of workers and safety supervision by a competent person are some of the basic requirements.
Precautions Prior to Demolition:
- A definite demolition procedure should be worked after studying the entire structure and carrying out a survey of its drawings, load bearing members, type of foundation, walls etc., chemical contents if any, previous use, structural problems, ground characteristics, condition of roof trusses, type of framing used in framed structure, equipment sensitive to noise, vibration, dust etc. radioactivity, utility or service lines, gas and power lines, joint with or effect on adjacent building, climatic conditions etc. A help of structural engineer is advisable.
- Formulate a method of demolition after above survey and record in a method statement after identifying the problems and their solutions accordingly.
- Shut off all electric, gas, water and other service lines or protect it safely against damage. Isolate the plant or building from all other plants or buildings.
- For protection of the public, ensure fencing of all the roads and open area surrounding the work (i.e. danger or safety zone) (fence height at least 2 m) and display caution boards and danger signs in the local language, Hindi and English at prominent places.
- Control unauthorized entry into it effectively.
- Whenever there is use of a swinging weight (ball) for demolition, width of the safety zone should be 1.5 times the height of the structure. If there is use of a clamshell bucket for demolition, Maintain safety zone of 8 m from the line of travel of the bucket.
Precautions During Demolition:
- Employ only trained workers (new or unskilled may cause more accidents).
- They should wear helmet, safety belt, safety shoes, safety goggles and gloves in construction site.
- Do not demolish a part which would destroy the stability of other parts.
- Adequately shore, brace or provide support to prevent danger, parts or structure.
- Do not demolish foundation walls serving as retaining walls to support earth or adjoining structures until underpinning or bracing the adjoining structure and the earth removed or supported by sheet piling or sheathing.
- Whenever using deliberate controlled collapse technique, obtain expert engineering advice. Use it only whenever enough surrounding space is available to withdraw men and equipment at a safe distance.
- Structure not carrying its design load may be pre-weakened before a deliberate collapse, but in such cases carefully plan the pre-weakening and reduce dead load systematically.
- When using of equipment such as power shovels and bulldozers for demolition, consider type of building its dimensions and the power of the equipment.
- Whenever there is use of explosives demolish key members, agree the blast protection and safe distances in advance. Only allow experienced personnel in a controlled manner.
- Sometimes catch platforms (at least 1.5 m wide) are provided along the outside of the outer walls to catch falling materials. The outer edge of such platform should be higher than the inner edge (i.e. inclined to wall side) and the platform should be lowered as the demolition work gets lowered.
Sequence of Demolition.
- Remove glass panels of doors and windows first. Then remove loose objects and projecting parts including balconies.
- Work should start at the top of the structure and proceed downwards. When work is going on at upper level, do not deploy workers at lower level.
- Do not allow to throw broken material but lowered safely. In addition, Do not allow to accumulate to disturb stability.
- Minimize dusting by watering simultaneously.
- Keep stairs with hand railing in place as long as practicable to provide access and egress.
- Use independent scaffolds for demolition with relation to structure. Use traveling mechanical ladders.
- AC sheet roofing requires careful consideration of points of support before planning its demolition. Provide a firm ladder resting on such point so that workers can climb to the roof. Then they should use a cat ladder or a crawling board supported on ridge to stand and remove the sheet.
- In no case, do not allow to walk or stand directly on the AC sheet. Underneath nearby use fall arrester net.
- Demolish walls storey by storey and starting from the top.
- Prevent unsupported walls from falling by shoring and ties.
- Demolish floors by using planking or walkways to stand or more when it becomes weak to withstand the load. Ensure fencing or barricading of openings through which material is to drop.
- Do not demolish tall chimneys by blasting or overturning unless the sufficient open area is available for its safe fall. Workers should not stand on chimney wall. Remove thrown down material during breaks in the work or under controlled conditions.
- Demolish structural steelworks by cutting its parts in such a way that it should not collapse, twist or spring suddenly.
- Demolish it tier by tier.
- Do not throw cut parts from a height in any case. Lower it down safely..
- Demolish industrial structure such as a nuclear power plant, hazardous chemical or petrochemical plant or a plant containing a plenty of asbestos material (e.g. insulation, AC sheets) only after consulting their respective experts or specialist engineer and taking all precautionary measures against their specific hazards. General rules are as stated earlier.
Health and Welfare of worker`s safety in construction Site
- Occupational hazards and diseases relating to construction work are mainly dust hazards (silicosis due to silica dust, Siderosis due to iron dust, Anthracosis due to coal dust and Cement Pneumoconiosis due to cement dust), noise and vibration, heat and humidity, electricity, hazardous chemicals, work at heights and depths (in a confined space), material handling, lifting machinery, transport vehicles, radiation hazards, biological hazards etc. First-aid boxes and occupational health services at workplace or nearby are most desirable.
Dust Hazards:
- While handling building materials, workers can be exposed do four types of dusts which by inhalation can cause following lung diseases (pneumoconiosis):
- Silicosis: Silica (SiO2) dust (respirable size 0.5 to 3 micron) causes fibrotic changes, modulation in both lungs, shortness of breath, decreased chest expansion, reduced capacity for work and in advanced case impairment of total lung capacity. Moreover, the effect is irreversible and no effective treatment is available. Specifically, It is a notifiable and compensable disease under the law.
- Overall, the effect of exposure, varies with the concentration of dust, time period, working conditions, body resistance, control measures etc.
- Chest X-ray shows a snow storm appearance in lung field. But confirmation requires by a history of prolonged exposure of silica dust and symptoms of dry cough, dysponea, chest tightness and difficulty in breathing. Although, Regular medical examination of workers and engineering controls to minimize exposure are necessary.
- Siderosis is caused due to inhalation of iron dust (iron oxide). For Example, due to Electric arc welding, dry grinding of iron, buffering, polishing and shot-blasting produce iron dust. It seldom causes serious symptom unless there is co-existent silicosis.
- Anthracosis (Coal workers’ pneumoconiosis) is caused due to inhalation of coal dust. For example, Foundry workers, coal handlers, couple collie, boilermen (scalers), furnacemen, railway firemen, graphite workers etc. are exposed to coal dusts. The first phase (requires about 12 years of work) causes little ventilatory impairment, but the second phase causes progressive massive fibrosis (PMF) resulting in severe respiratory disability and tending to death.
- Early diagnosis and change in occupation obviously offers the best hope. For Example, other treatment like chemotherapy should be as per doctor’s advice.
- Cement (Benign) Pneumoconiosis, silicosis with associated pulmonary tuberculosis, bronchitis and emphysema are possible with cement or cement and free silica dust (e.g. acid resistant cement).
- In addition to these respiratory disorders, other health hazards are as under:
Skin | Cement eczema due to alkalinity or presence of chromium, Furuncles, Pyoderma, Cellulitis, Asbestosis |
Vision | Conjunctivitis |
Nervous system | Muscular pain, Back pain, Neuralgia, Spondylosis, Arthritis and Rheumatism |
Digestive system | Peptic ulcers |
Ear | Hearing loss due to high noise |
Others | Radiant heat, High temperature near furnace, CO gas and Asbestosis due to asbestos cement products |
- Prophylaxis (Control measures) are engineering control and medical monitoring.
- Generally use engineering control includes methods of elimination or minimization of dust exposure, local exhaust (suction hood), cyclone dust collector, unit dust collector, electrostatic precipitators, substitution of wet grinding for dry grinding and hydro-blasting for sand blasting and built-in devices with grinding and polishing machines etc.. Maintain them in good working conditions. Workers should wear dust masks/respirators and eye protection also.
- Medical monitoring includes appraisal of dust generating places or processes, are monitoring and analysis, medical examinations including X-ray and sputum test, lung function test and clinical tests accordingly.
Noise and Vibration:
- Significantly, Crushers, grinders, compressors and heavy lifting machinery in construction site cause high noise.
- Continuously working near such high noise causes hearing loss, deafness, annoyance, change in heart rate, blood pressure, sweat rate, work performance etc. and also psychological and psychomotor effects.
- High frequencies are more serious than low frequencies.
- Also, Keep Noise level below 90 decibels by using quieter machinery and processes, enclosures and silencers.
- All things considered, give ear plugs or muffs of good quality to workers.
Heat and Humidity:
- Steel mills, forge shops, furnaces, boilers, hot asphalt, tar, steam, hot water, damp clay, under-water work etc. expose heat or humidity.
- In dry hot atmosphere, Maintain thermal balance by evaporation of sweat but in moist hot atmosphere as in cotton mills, process of perspiration (sweat evaporation) slows down due to humidity and workers feel great discomfort and their productivity gets down due to heat stress.
- Basically, Main three types of heat stresses are heat stroke, heat exhaustion and heat cramp.
- Insulation of hot processes and parts, lagging of hot pipes, shielding against radiant heat, local exhaust ventilation, improvement in general (natural or mechanical) ventilation, spot cooling of hot object, isolation or segregation of hot processes, replacement of workers near furnaces or giving frequent recesses and adequate supply of drinking water are some of the remedial measures.
Other Hazards:
- Fire hazards due to use of solvents, thinners, paints, varnishes etc.
- Use of chemicals, pigments, radioactive substances and biological agents pose peculiar types of hazards.
- Ensure work permit and special precautions when workers have to work at height or in a confined space.
First-aid and Health Services:
- At all work sites, first-aid boxes containing prescribed medicines, antidotes and equipment are of equally important.
- Ensure employment of only trained first-aiders accordingly.
- They should be proficient in the use of resuscitation and other life-saving techniques and also in rescue procedures.
- Necessary equipment including stretches should be readily available.
- All workers should be subject to health surveillance regardless.
- Carry out work area monitoring with this purpose in mind.
- Health services should be available at workplace or nearby.
- It also requires medical examination, construction medical officer, OHC, ambulance room, ambulance van, stretches, FAB, emergency treatment notice of occupational diseases etc.
Welfare:
- At or near work site, adequate supply of drinking water, sanitary and washing facilities or showers, change or cloak room, lunchroom or canteen, rest room or shelter, facilities for food and drink and suitable living accommodation should be available to workers indeed.
- The size and number of such facilities may vary accordingly to the number of workers.
- It is equally important to provide separate facilities for male and female workers where necessary.