Effective Strategies for Accident Prevention
Definition:
- Accident is an unplanned, unexpected, unwanted, unforeseen, undesired, unintentional event or consequences of the event which could have resulted in injury, property damage or both.
- Event or consequences of event that do cause harm or damage accordingly.
- These are often called LOSS-TYPE INCIDENTS.
Some facts about accidents:
- Accidents bring loss in form of human injury/loss, property damage/loss.
- Each and every accident takes place due to consequences of abnormal event, which can be find out by proper investigation.
- Mostly it caused by unsafe act and unsafe condition.
- Although It is preventable by controlling or removing unsafe act and unsafe conditions.
- All accidents are preventable by proper prevention techniques.
- Accident caused, it just not happened.
Consequences of Accident:
It can cause :
- Human Injury in terms of permanent or temporary disablement. Moreover, family of victim suffers.
- Loss of Life which makes victim family suffers.
- As a result of injury, there is loss of income.
- Insurance cost.
- Property damage.
- Production loss because of work stoppage.
- Legal proceedings.
- Affects reputation of the company.
- Local surrounding issues.
Effective Accident Prevention Strategies or Methods :
- Hazard Identification And Risk Assessment (HIRA) for all activities performed and to be performed accordingly.
- Preventive measures or controls to all identified Hazards and Risks.
- Regular safety inspections, safety surveys, safety audits, Mock Drills etc. and rectification of gap identified.
- Training to all resources for safe working method.
- Awareness about hazard and related precautions in workplace.
- Safety signage, work permit system, SOPs, Safe work method statements, MSDS etc. proven to be good effective accident prevention strategies.
- Work as per Safe Operating procedure, and strict implementation.
- Reporting and communication of all near-miss, accidents, incidents to prevent reoccurrence of the accident.
- Maintain Good House Keeping.
Types of Accidents:
Based on severity of injury, accidents are major, minor or near miss type. The combination of injury and property damage gives four types of accidents as follows:
- Injury and property damage (major).
- Injury and not property damage (major or minor).
- Property damage and not injury (major or minor).
- No property damage and no injury (near miss).
Based on causation, Accident are of five types:
- Psychological causes –
inexperience, not motivated for safety, worry, emotional, wrong attitudes etc. - Physiological causes –
age, sex, body-build, poor hearing, vision, strength etc. - Physical causes –
heavy workload, long working hours, no rest, unhealthy work environment, work at height, depth or in confined space, falling load etc. - Mechanical, Electrical, Chemical, Radiation causes –
unguarded machinery, defective equipment, noise, vibration, obstructed pathway, sharp edge, electric shock, static electricity, chemical, poison, toxic gas, acid, fire, explosion, radiation etc. - Environment causes –
weather effects, heat, cold, humidity, air, wind, rain, tide, lightening etc.
Causes of type No. 1 and 2 give rise to unsafe action while No.3 to 5 give rise to unsafe conditions.
Fundamentals of Accident Prevention:
- As explained by Heinrich, accident prevention is both, science and art. It represents control of performance of man, machine and physical environment.
- The word ‘control’ includes prevention as well as correction if unsafe conditions and actions. Prevention is the first or initial part of ‘control’ which if practiced, subsequent control for consequence or effect may not be needed. Thus accident control is a vital factor in every industry, which if ignored or practiced unskillfully, leads to needless human suffering and business bankruptcy.
- The accident-prevention task requires both, the short term approach (direct control of personal performance and environment) and the long-tern approach of instruction, training and education. This task must be performed before an accident and injury occur. Subsequent efforts after accidents are also necessary.
- Thus effective accident prevention strategies may be defined as an integrated programmes, a series of coordinated activities, directed to the control of unsafe acts and unsafe conditions and based on knowledge, attitude and ability for safety. It aims to serve industry, country and humanity.
Five basic or fundamental steps for effective accident prevention strategies(Safe and efficient production), Suggested by H.W. Heinrich, are:
- Organization.
- Fact finding.
- Analysis of the facts found.
- Selection of remedy and
- Application of the remedy.
1. Organization:
- The safety organization, management or at least the planned procedure, which it represents, is the vehicle, the mechanism by means of which interest is kept alive and the safety programme is designed, directed and controlled. The actual work of prevention is done by safety director or manager, safety officer and the line and staff supervisors with the active support of top management.
- Safety is not only a staff function but it is a line function also. Budgetary provision (cost allocation) for safety should be made from very beginning.
- Here organization does not mean safety department only. Safety is not a function of one department only. All the members of organization (including all departments) have to contribute and play their role for safety.
- Basic philosophy and safety policy for effective accident prevention strategies and firm determination of the top management are utmost necessary.
- Organization also includes single person working for safety.
2. Fact Finding: The knowledge of probable or potential hazards (facts) is derived from surveys, inspections, safety audits, observations, review or records, inquiry, investigation and judgment.
- Facts include the past, prevent and future facts which have caused and which can cause accidents. Past causes can be known by ‘accident records’ and inquiry. Future (hidden) causes can be known by HAZOP, HAZAN, safety audit, inspection etc.
- The term “hazard” is synonymous with the phrase “direct and proximate accident cause” i.e. the unsafe personal act and/or unsafe physical, mechanical, electrical, chemical, environmental condition without which no accident can occur.
- Personal hazards (unsafe acts) are violations of commonly accepted safety rules, practices and procedures. Mechanical hazards (unsafe conditions) are of four groups: Static, kinetic, electrical and chemical (including radioactive or nuclear).
- There are some general heads or categories under which grouping of more specific acts. For example, sub-itemization of the general head “Making safety devices inoperative” can as:
- Removing guards.
- Tampering with adjustment of guard including making interlock guard inoperative.
- Beating or cheating the guard.
- Failing to report defects.
- etc.
Discussion about Two types of main facts – unsafe acts and unsafe conditions – are as below.
1. Unsafe Acts:
Unsafe act is a human action resulting in accident or injury to him, others, environment or all.
Some reasons of unsafe acts are as under:
Improper Attitude
- Willful disregard, reckless, lazy, disloyal, non co-operative, fearful, oversensitive, egoist, jealous, impatient, absentminded, excitable, obsession, phobia, inconsiderate, intolerant, mentally unsuited and other psychological reasons.
Lack of knowledge or skill
- Insufficiently informed or trained misunderstands, not convinced of need, indecision, inexperienced etc.
Physically Unsuited
- Due to hearing, sight, age, sex, height, ill, allergic, slow reaction, crippled, intoxication, physically handicapped and other physiological reasons.
Physical Conditions
- Space, light, ventilation, heat, layout or arrangement, materials, tools, equipment, procedures, company policy, routing etc. make it awkward, difficult, inconvenient, embarrassing or impossible to follow safe-practice rules.
- Notice Unsafe act as early as possible and remove it just after it comes in notice. Purpose should be of removing injury, to prevent recurrence and not to punish any individual.
- Observation of Workers should be proper for their unsafe act by seeing their selection and use of –
- Position of their standing and working.
- Tools and equipment including hand tools, power tools, lifting tools, PPE, FFE etc.
- Method or procedure adopted by them.
- Traffic and driving rules.
- Position and working should not be in dangerous conditions. Tools and equipment should be of correct size and type, usage of same should be correctly and in right condition. Procedure or method should be safe and adequate. Where there is requirement of safety work permit, it`s explanation and implementation must be correctly. Driving should be safe or must follow defensive and traffic rules. Drivers of vehicles of hazardous goods should have undergone specific training.
- After seeing an unsafe act, observer’s (e.g. supervisor or safety officer) attitude should be to ‘talk with’ the worker and not to ‘talk to’ the worker. This means to call or advise the worker politely, ask him why he is doing so or not using required tool, equipment, procedure etc, hear his explanation, try to understand him and then explain him the ‘underlying hazard’ and make him convinced about ‘unsafe act’ and to correct it as per safety requirement.
2. Unsafe Conditions:
- Creation of Unsafe condition by an unsafe act of a person or act of God or any agency or due to failure or weakening of any material, structure, situation, condition or system.
- Observance of unsafe conditions includes many areas such as proper lighting, ventilation, housekeeping, floors, platforms, handrails, toe guards, machine guards, tanks, vessels and pipelines, safety fittings and devices, electrical hazards, fire prone condition, gaseous and dust exposures, noise, vibration, heat or atomic radiation, loading, unloading and transportation etc.
- Such unsafe conditions are due to non-provision, non-maintenance, poor-maintenance, poor-supervision, lack of training, improper design and layout of plant & machinery, poor lighting, poor ventilation, absence of guards and safety devices, failure of safety devices, equipment or tools, unsafe structure, poor housekeeping, fire-prone area, sources of ignition, static electricity, slippery floor, high noise, vibration, radiation etc.
- Observation for unsafe working conditions should include basic techniques of look, listen, smell and feel (LLSF) to detect unusual condition of situation, position, noise vibration, odour, temperature, pressure, out of control etc.
3. Facts from Accident Reports:
- Form No.21, 21 A and 29, under the Gujarat Factories Rules and Annex-13 under the Electricity Rules prescribe some facts for accident reporting which reference should be available for information accordingly.
- Facts should include ‘past facts’ of accidents already happened and ‘future facts’ of possible accidents based on various hazard identification techniques such as Hazop, Hazan, risk assessment, Fault Tree Analysis (FTA), Event Tree Analysis (ETA) etc.
3. Analysis of the Facts:
- The third step to effective accident prevention strategies is analysis of the findings. This is defined as the work of drawing conclusions from assembled data. The hazards are here named, identified and classified or analyzed. To do such work by (a) analysis of past experience (b) Survey and inspection (c) Judgment and experience plus enquiry. Identify the direct causes, sub-cause, underlying major causes, types of accident, operations, tools and equipment, obstacles, frequency, severity, location, occupation etc., and classify them.
- The supervisor’s report of accident investigation is the basis of all analysis of past and present accidents. It is the most important, difficult and skillful task requiring good knowledge and experience. Decide very carefully that which is the unsafe act, which is the unsafe condition, which is more proximate and the accident is due to any one or their combination and in which sequence. From facts, witnesses and rational judgement find reply to all these questions and report properly for real accident reporting and true causation study.
Twelve steps (safety officers’ procedure) to analyze the causes of accidents are as follows:
- Obtain the supervisor’s report of the accident containing the details given above.
- Obtain statutory accident report form.
- Obtain the injured person’s report.
- Obtain the reports of witnesses if any.
- Obtain the doctor’s report on injury.
- Investigate the accident.
- Record all evidences and facts. Tabulate the essential facts of the accident together with the similar past accidents.
- Study all the facts.
- Analyze accident causes in details. Such analysis will classify causes as defective or no guard, poor lighting, poor ventilation, no safety devices, no use of PPE, accidents – fatal or nonfatal, male or female wise, day or night wise, age wise etc.
- Arrange the causes in order of importance or priority of compliance.
- Find and record reasons of existence of those causes.
- After finding potential, hazards, cross analysis of records must make to select most important hazards or targets. Reasons for existence of hazards must be found for correction.
4. Selection of Remedy:
When it is analyzed to indicate which is the proximate or main cause that needs to be corrected then it suggests the fourth step of selection of remedy for the named (analyzed) hazards. Four basic remedies are as under:
- Engineering Controls: Guarding of machine and tools, isolation of hazards, revision of procedures and processes, good illumination, ventilation, colour and colour contrast, substitution of safer materials and tools, replacement, reduction, repair and a variety of mechanical, physical and chemical remedial measures.
- Instruction, Training, Persuasion and Appeal: Regular training as well as instruction, reinstruction, persuasion, appeal, notice, posters, supervision and motivation.
- Personnel adjustment: Selection and placement with regard to the requirement of the job and the physical and mental suitability of the worker, medical examination, treatment, advice and PPE.
- Discipline: Mild admonition, expression of disappointment, fair insistence, statement of past record, transfer to other work and penalties.
- In the process of selecting an effective remedy, ‘Engineering Control’ takes the first place and discipline as the last resort. Select the most effective and urgent remedy first and then precede priority wise.
5. Application of the Remedy:
The final step in effective accident prevention strategies is application of the selected remedy.
- If machines, tools, vessels, equipment, structures, procedures etc. are unsafe, we must guard them, replaced, revised or otherwise made mechanically safe or accident free. This is management’s responsibility. The safety officer/engineer will guide and the supervisors see to it that they do necessary work.
- If the personal performance is unsafe, selection of employees is must, instructed, trained, cautioned, persuaded, convinced and appealed for improvement. Certain cases require proper placement, other medical or psychological treatment or advice. In rare cases and as a last resort, need to take some form of disciplinary action.
- Application of selected safety measures should be immediate and long-term. Existing unsafe conditions and actions should be corrected at once while at the same time long-term programmes should be started to include procedures and techniques devised to anticipate and prevent situations of a similar nature.
- Application of remedy is the dynamic part of accident prevention. Unless successful application of the remedy, all prior steps are of no use and wasted
1. Ways & Means of Application of Remedy:
A safety engineer or officer applies the following ways:
- Prepares, presents and applies recommendations, suggestions, summaries and plans.
- All in all, Establishes a safety organization.
- Therefor, Gets support of management and supervisory staff in applying the remedies.
- Creates enthusiasm and co-operation up and down the line.
- Satisfies himself by seeing the successful working of the remedies applied.
- He will apply in chronological order the four basic remedies. Engineering controls call for designing, buying and building, installing and maintaining guards, safety devices and safety equipment. The persuasion and appeal remedy requires teaching, training, appeal, instruction, persuasion etc.
- He must have ability to overcome obstacles in applying remedies. He should identify the obstacles as a person, attitude, condition or circumstances.
- Constant follow-up action through safety administration is necessary. Detection and placement of physically impaired workers should be carried out carefully and effectively. In a typical one-man plant the employer himself has to carry out all such functions single-handedly. Expect All employees are going to work safely. Responsibility should be fixed and distributed for quick compliance. A supervisor or foreman is the key-man for such purpose.
- Control Machine –accidents by effective engineering – revision. Also many accidents take place in material handling for which two highly successful methods may be employed.
- (i) One lies in the study and improvement of methods and procedures to the end that some safer and better way or equipment may be found to conduct any particular operation than that in use.
- (ii) Secondly, it is most useful to utilize the proper degree of supervision – from the chief executives down to the foreman – that will result in the observance and correction of unsafe material handling practices on the part of the workers before injuries occur.
2. Creating and Maintaining Interest:
- The second basic remedy of persuasion, appeal, instruction and training requires vast efforts. The practice of creating and maintaining interest for effective accident prevention strategies applies to employers as well as employees.
- Creation and maintenance of group interest of employees by the safety organization which includes moral and educational effect or accident investigation, publicity, posting and distribution of educational literature, safety films and slides, contests, prizes, awards, meetings and inspirational talks.
- Creation and maintenance of individual interest of employees by an appeal to personal characteristics listed below:
- Self-preservation (Fear of personal injury): Featuring the injury by figures, posters, notices, meetings, oral discussion, lectures, films and slides are useful to maintain the strongest and commonest human instinct of self-preservation or self-protection.
Personal and material gain (Desire for reward):
- Bonus, salary increase, vacation with pay, days off, trips, personal gifts, requisite assignments of work, banquets, picnics and participation in safety activities prove useful in this regard.
Loyalty (Desire to co-operate):
- Effect of accident by the employees on supervisor’s record, on employer’s overhead cost, on quality of product, on fellow employees and on company’s prestige must be brought to the notice of individual to create and maintain their sense of loyalty to the employer.
Responsibility (Recognition of obligation):
- Creation of the sense of responsibility, both to self and to others, is by assignments and analogy of observance of safety rules.
Pride (Self satisfaction and desire for price):
- Pride increases ability to work. Praise exhibits, awards and insignia, differentiation of workers having outstanding safety record by giving them special hat/dress, reward etc., are useful in this regard.
Conformity (Comparison with standards or good examples):
- Some methods of appeal are: Standards (Safe practice rules, codes, procedures etc), comparison, system and regularly, leadership of good example in safe conduct, ridicule, etc.
Rivalry (Desire to complete):
- Man is a highly competitive animal and creates better results when competing with other than when working alone. For this, provide opportunity, set up objectives and determine method of measurement.
Leadership (Desire to be outstanding):
- The desire for leadership is strong in many persons which may be used to advantage in safety work. Give additional responsibility to such persons in safety work and promotion etc.
Logic (Special ability to reason):
- Some persons have special ability to see both sides of a question and to arrive at conclusions that are logical and just. Use such persons in safety work. A few methods of appeal to logic are basic philosophy of accident causation and prevention, providing data relating to accident frequency, severity, types and causes of accidents and remedial measures.
Humanity (Desire to serve others):
- Humanitarianism is a widely spread human instinct and strong appeal to everybody for safe performance. Safety is termed as human engineering on this ground where expect human to be at Centre. We have to fit the unfit to survive.
3. Education:
- All accident-prevention work is basically educational. Well-trained and careful men may avoid injury on dangerous work and untrained and careless men may be injured under the safest possible conditions.
- Safety education is meant to include meetings and talks, personal contacts with authorities or teachers, use of bulletins, posters, lectures and reading materials, slides and films, computers, first-aid instructions and any oral or written instructions for avoiding hazards and cultivating safe methods of doing work.
- List of some of the most commonly used educational procedures are as below:
- Regular safety coaching class for workers. Explanations of Hazards, safety precautions, safety measures, safety duties and procedures should be in their own language.
- Periodical safety class for supervisors, managers and top executives for coordinated efforts from all.
- Safety meeting, conference, seminar, exhibition etc.
- Publicity-Safety posters, slogans, maxims, notices, bulletins, pay-pocket-inserts, stickers, slides, films, house magazine etc.
- Safety books, pamphlets, periodicals etc.
- Safety contests, essays etc.
- Safety plays and similar programmes.
- Preparation of safety codes, standards etc.
- Use of loyal employees in setting a good example.
- Safety message on work orders, computers, correspondence etc.
- Featuring specific safe-practice rules.
- Investigation of accidents and explaining their analysis of unsafe actions, unsafe conditions and their remedial measures.
- Conducting training programmes.
- Sending persons to outside safety courses.
- Specific programmes as per our own need and nature of work.
- Conducting short-term safety course for all employees in rotation.
3. Models for Accident Prevention:
H.W. Heinrich’s model of ‘Five steps of accident prevention’ is explained previously.
1. Kepner-Tragoe Model:
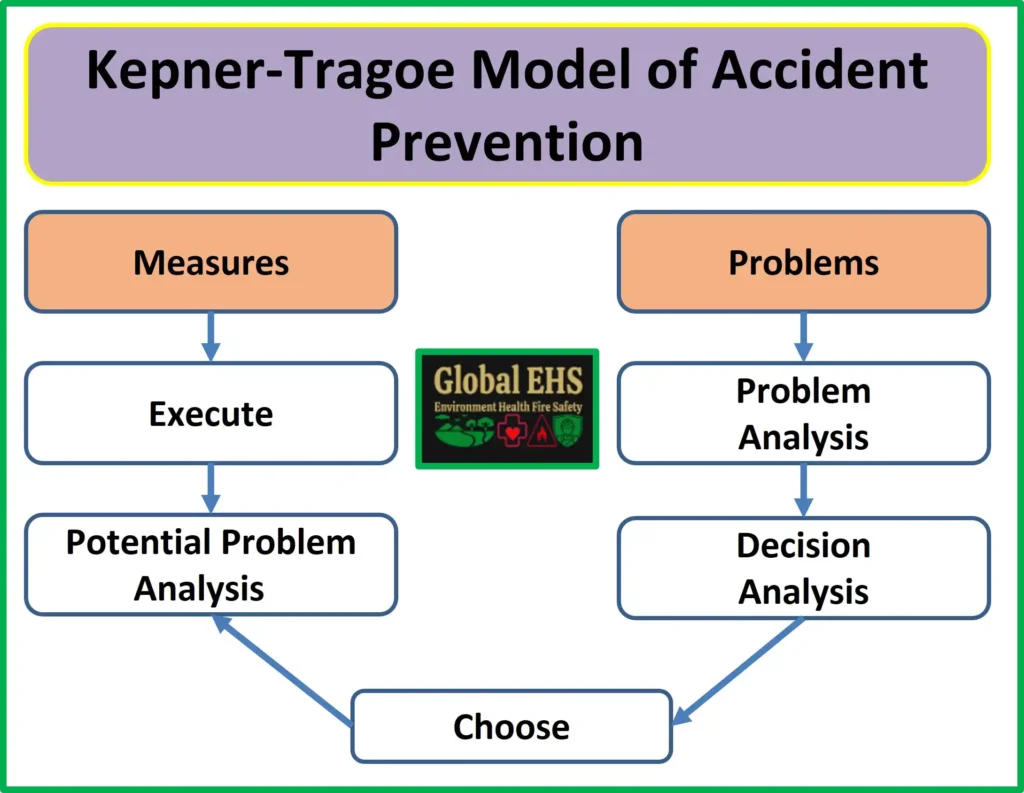
- ‘Execute’ means application of remedy.
- ‘Measure’ is a new step in this model, requiring measurement and monitoring of the execution.
2. Improving Human Performance (Error Reduction) Model:

- Discussion about this model by Johnson in MORT (Management Oversight Risk Tree). Here considerations of errors are inevitable, situations error-provocative, rate of error measurable and reducible.
- Study, practice and participation can change situations.
3. Performance Cycle Model:

- Johnson has discussed this model in his MORT. Here five steps in sequence are problem, its analysis, decision, action and measurement of result.
- Analyze it again for re-decision.
4. Updated Safety Management Model:
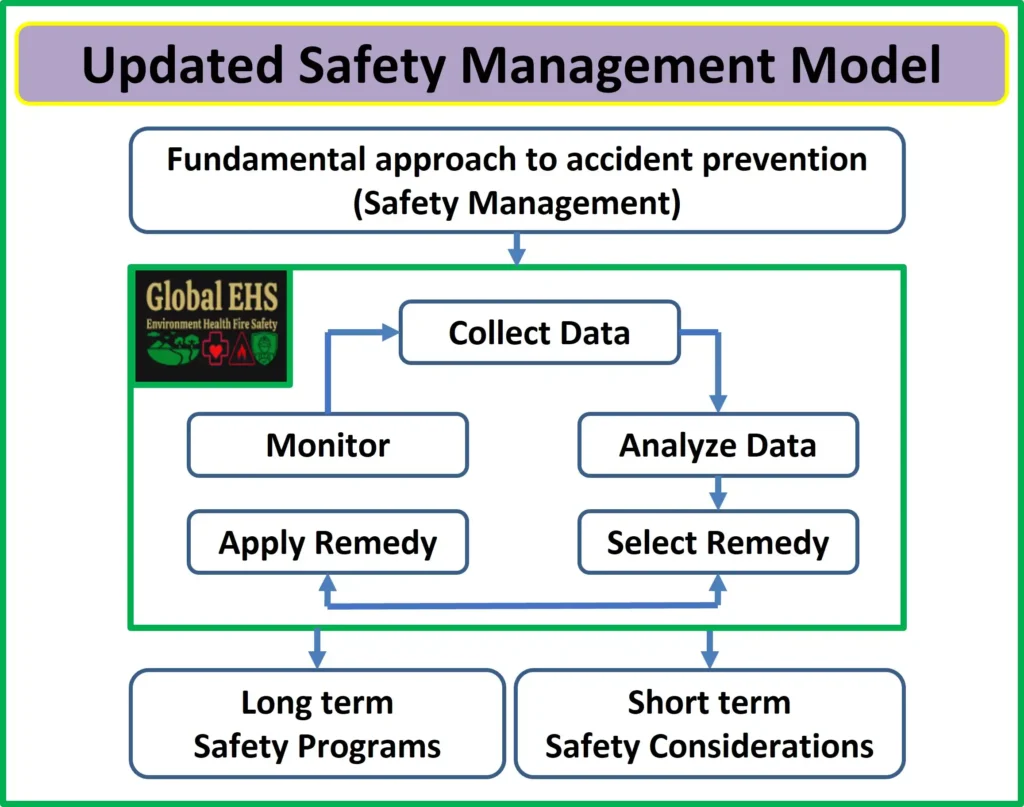
- This is updated model of Heinrich’s five steps model shown in Fig. Here only one step of ‘monitor’ is added for monitoring of applied remedy and to reconsider the problem.
- Requirement of basic philosophy of effective accident prevention strategies is at the root of any safety management. Monitoring is a feedback mechanism, it tells us how we are doing, what progress we are making.
- It dictates additional needs, we then collect additional data, analyze it, select additional remedies, apply them, monitor and so on.
4. Five ‘E’ s Accident Prevention
Achievement of safety or effective accident prevention strategies can be by the following five methods:
1. Education & Training (To prevent unsafe acts)
- This has long-term and permanent effect. This is the most powerful remedy for unsafe act of the workers. It helps in finding out unsafe conditions also.
- The workers’ safety training programmes should include (a) Understanding of specific hazards of their plant, process, building etc. (b) Safety rules and safe procedures (c) Training for specialized or difficult job (d) Job safety analysis and (e) Safety instructions for variety of jobs.
2. Engineering controls (to prevent unsafe conditions)
- Poor illumination and ventilation, unguarded machinery, mechanical, electrical, physical and chemical hazards, dangerous location or situation etc., are unsafe conditions which elimination is possible in the design stage or subsequent engineering revision and controls. This is the first and most effective remedy.
- Some engineering controls are – substitution of less hazardous material, machine, method, process, vessel etc. risk reduction, process modification, isolation, segregation, guarding, fencing, barricading, enclosure, dilution, safe design, failsafe device and safety devices including alarms, trips, safety valve, NRV, PRV, FFE, etc.
3. Enforcement (of safety rules)
- Need to follow all statutory safety provisions for our own safety and safety of others. Self initiation for full compliance is necessary, otherwise government authorities may take action.
- In addition, Define and follow other safety rules for our plant. Strictly deal with willful neglect or disobey of safety rules or orders.
- Enforcement measures include – new law, amendment in old law, company safety rules, implementation and legal action.
4. Enthusiasm (to maintain interest)
- Like a catalyst it adds to safety awareness and motivation. It should come from the top management to the lowest worker.
- It will keep the workers safety conscious. Development and maintenance of it can be by proper safety attitude, competition, prizes, awards, publicity, incentives etc.
- This includes motivation and participation in safety programmes
5. Example setting (to lead for safety)
- The top executives, managers and supervisors should set an example to others by the self-enforcement of safety rules.
- Then others will follow them. This is a chain reaction to increase and maintain safety.
5. Approaches to Preventive Action:
1. Proactive or Preventive Approach (Effort before accident)
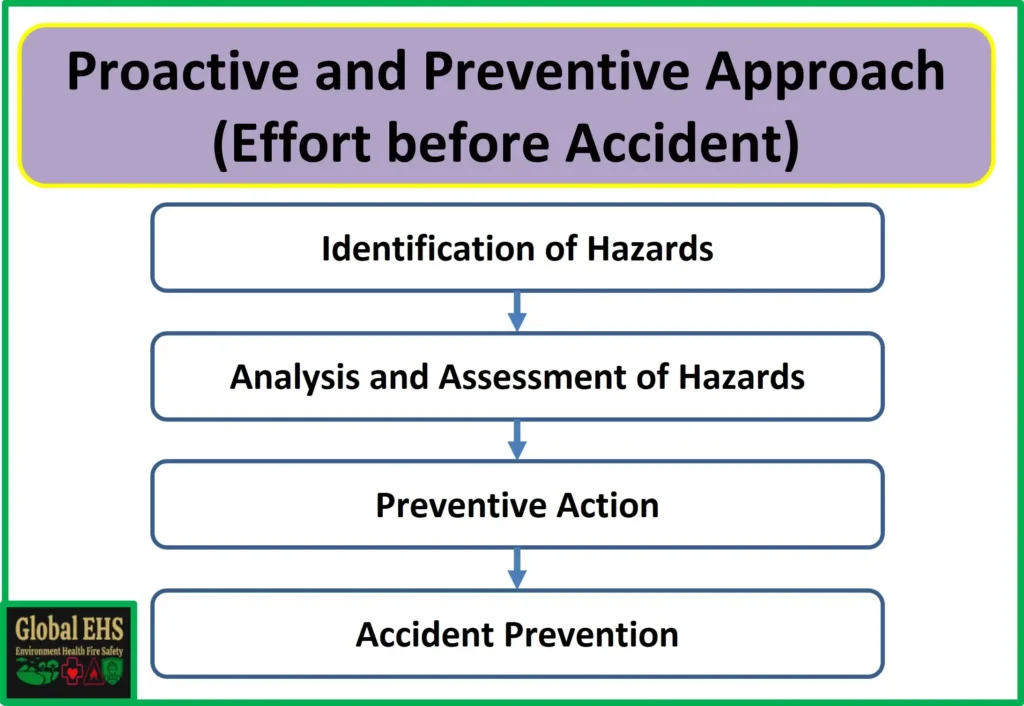
- In proactive or preventive approach, starting of without waiting for accident. Potential hazards are first identified, analyzed and preventive programme is formulated to remove or reduce the hazards identified.
- This approach is better then the reactive approach, but it incurs regular costs.
2. Reactive or Corrective Approach (Effort after accident)
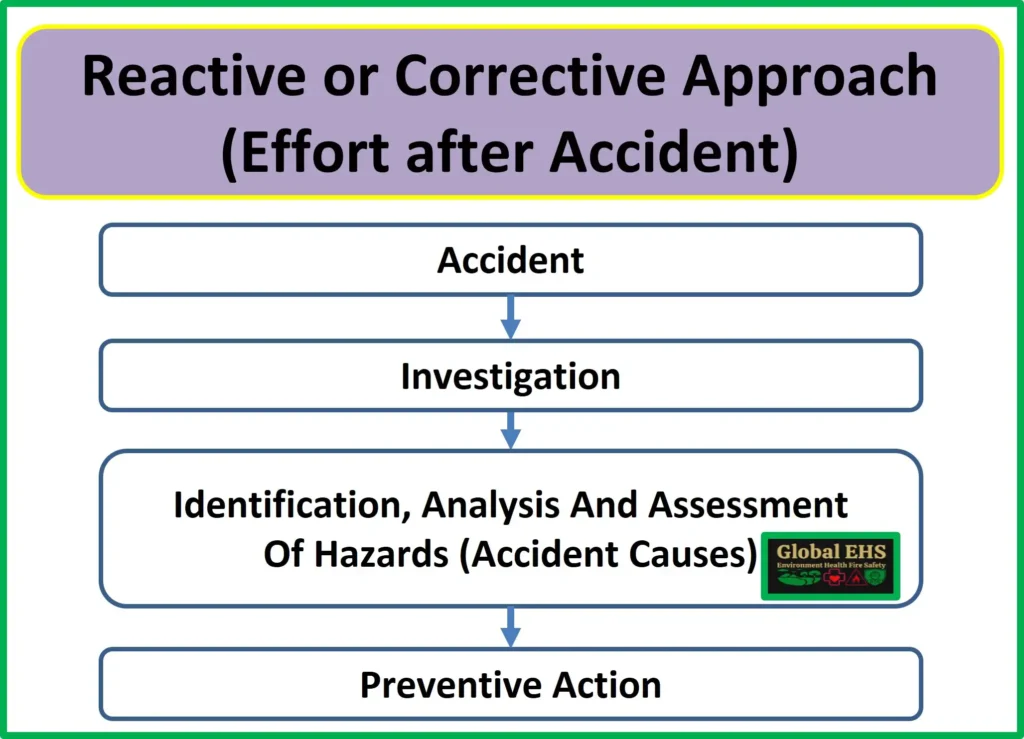
- Normal habit of a person or management is to follow this reactive or corrective approach only after an accident.
- They do not think to invest money or time for preventive measures to avoid accidents by advance planning. Drawback of this approach is to suffer some loss due to one or more accidents.
- In this approach, Starting of action is after accident. Analysis of investigation of accident causes and determination of preventive action done.
- Then application of it is to prevent recurrence of the similar accident. This works as a lesson from the accident.