Understanding and addressing hazards of power tools through proper training, risk assessment, and implementation of safety measures is essential to prevent accidents and injuries when using power tools.
Here is the list of hazards of power tools;
1. Electrocution:
Improper grounding, damaged cords, or contact with water can lead to electric shock or electrocution when using electric-powered tools.
2. Lacerations and Amputations:
High-speed rotating blades, saws, and other sharp components can cause severe lacerations or amputations if they come into contact with the body.
3. Strain and Repetitive Stress Injuries:
Prolonged use of power tools, especially those requiring forceful gripping or repetitive motions, can lead to strains, sprains, and other musculoskeletal injuries.
4. Impact Injuries:
Tools such as pneumatic nail guns or impact wrenches can cause injuries from flying debris, accidental discharge, or tool kickback.
5. Falls and Trips:
Power cords, debris, or uneven surfaces in the work area can lead to slips, trips, and falls, especially when using handheld power tools or working at heights.
6. Dust and Fume Exposure:
Grinding, cutting, and sanding operations generate dust, fumes, and airborne particles that can pose respiratory hazards if inhaled, leading to lung damage or respiratory illnesses.
7. Noise-Induced Hearing Loss:
High noise levels generated by power tools, such as drills, saws, and grinders, can lead to permanent hearing loss if proper ear protection is not used consistently.
8. Vibration-Induced Injuries:
Tools like jackhammers or rotary hammers can transmit vibration to the hands and arms, leading to hand-arm vibration syndrome (HAVS) or other nerve and circulatory disorders.
9. Chemical Exposure:
Power tools used for tasks like painting, stripping, or applying coatings may involve exposure to hazardous chemicals, leading to skin irritation, respiratory problems, or long-term health effects.
10. Fire and Explosion Risks:
Tools that generate heat or sparks, such as angle grinders or welding equipment, can ignite flammable materials or explosive atmospheres if used improperly or in hazardous environments.
11. Eye Injuries:
Flying debris, sparks, or particles generated during cutting, grinding, or drilling operations can cause eye injuries if proper eye protection is not worn.
12. Crushing Injuries:
Power tools with heavy components or moving parts, such as hydraulic presses or power saws, can cause crushing injuries if body parts are caught between them.
13. Chemical Burns:
Exposure to corrosive chemicals or solvents used in conjunction with power tools, such as adhesives or cleaners, can cause chemical burns if they come into contact with the skin.
14. Heat and Fire Hazards
Overheating of power tools, electrical malfunctions, or contact with hot surfaces can lead to burns or ignite flammable materials, posing fire hazards.
15. Electric Shock from Faulty Equipment:
Malfunctioning or poorly maintained power tools may develop electrical faults, increasing the risk of electric shock to users.
16. Pinch Points:
Power tools with moving parts, such as chainsaws or power presses, can create pinch points where fingers or other body parts can become trapped, resulting in injuries.
17. Explosive Atmospheres:
The use of power tools in environments with combustible gases, vapors, or dusts can create explosive atmospheres, increasing the risk of ignition and fire.
18. Ergonomic Hazards:
Poorly designed power tools or improper work practices can lead to ergonomic hazards, such as awkward postures, repetitive motions, or excessive force, resulting in musculoskeletal disorders.
19. Tool Kickback:
Power tools like circular saws or angle grinders can experience kickback, where the tool’s blade or disc suddenly jerks back towards the user, causing loss of control and potential injuries.
20. Inadequate Training and Supervision:
Lack of proper training, supervision, or experience in using power tools can lead to accidents, injuries, and unsafe work practices.
21. Tool Malfunction:
Power tools can malfunction due to defects, wear and tear, or improper maintenance, leading to unexpected behavior and potential accidents.
22. Flying Objects:
Tools like grinders or rotary tools can eject debris or projectiles at high speeds, posing a risk of injury to nearby individuals.
23. Unintended Activation:
Accidental activation of power tools, such as a trigger being bumped or a switch being left on, can result in unexpected starts and potential injuries.
24. Overexertion:
Some power tools require significant physical effort to operate, leading to fatigue, strain, and increased risk of accidents, especially during prolonged use.
25. Inadequate Lighting:
Poor lighting conditions in the work area can obscure hazards and increase the likelihood of accidents when using power tools, especially in dimly lit spaces or during night work.
26. Improper Use of Extension Cords:
Incorrect use of extension cords, such as using cords that are too long or damaged, can pose electrical hazards and increase the risk of tripping or entanglement.
27. Inattention and Distraction:
Distractions or lack of focus while operating power tools can lead to errors, accidents, and injuries due to the user not being fully aware of their surroundings or the tool’s operation.
28. Unsafe Work Environments:
Working in confined spaces, at heights, or in areas with limited ventilation can increase the risk of accidents and injuries when using power tools, requiring additional precautions and safety measures.
29. Inadequate Personal Protection:
Failure to wear appropriate personal protective equipment, such as gloves, safety goggles, or hearing protection, can leave users vulnerable to various hazards associated with power tool operation.
30. Inadequate Supervision of Novice Users:
Novice users or individuals with limited experience operating power tools may require closer supervision and guidance to ensure safe work practices and minimize the risk of accidents and injuries.
31. Chemical Exposure from Lubricants and Coolants:
Power tools often require the use of lubricants or coolants to maintain optimal performance. Exposure to these chemicals can pose health risks, such as skin irritation, respiratory issues, or chemical burns if proper precautions are not taken.
32. Hand-Arm Vibration Syndrome (HAVS):
Prolonged use of vibrating power tools, such as jackhammers or sanders, can lead to hand-arm vibration syndrome, characterized by symptoms like numbness, tingling, or reduced grip strength in the hands and arms.
33. Improper Storage and Handling:
Incorrect storage or handling of power tools, such as leaving them in damp or humid environments or storing them with their cords tangled, can lead to damage, deterioration, or electrical hazards.
34. Tool Overheating:
Continuous use of power tools without allowing them to cool down can cause overheating, leading to reduced performance, premature wear, or even the risk of fire or electrical malfunction.
35. Failure to Use Safety Features:
Some power tools are equipped with safety features such as blade guards, safety switches, or kickback prevention mechanisms. Failure to use or properly engage these safety features can increase the risk of accidents and injuries.
36. Inadequate Risk Assessment:
Failing to conduct thorough risk assessments before using power tools can result in overlooking potential hazards or underestimating the level of risk associated with certain tasks, leading to accidents or injuries.
37. Improper Tool Selection:
Choosing the wrong type or size of power tool for a particular task can result in decreased efficiency, increased risk of accidents, or damage to the tool itself.
38. Inadequate Maintenance:
Neglecting regular maintenance and inspection of power tools can lead to mechanical failures, decreased performance, or unexpected malfunctions during use, posing safety hazards to the user and others nearby.
39. Improper Tool Modifications:
Modifying or altering power tools in any way, such as removing safety guards or tampering with electrical components, can compromise their safety and functionality, increasing the risk of accidents and injuries.
40. Inadequate Emergency Preparedness:
Failing to have proper emergency procedures in place, such as knowing how to respond to injuries or accidents involving power tools, can delay appropriate medical attention and exacerbate the severity of injuries.
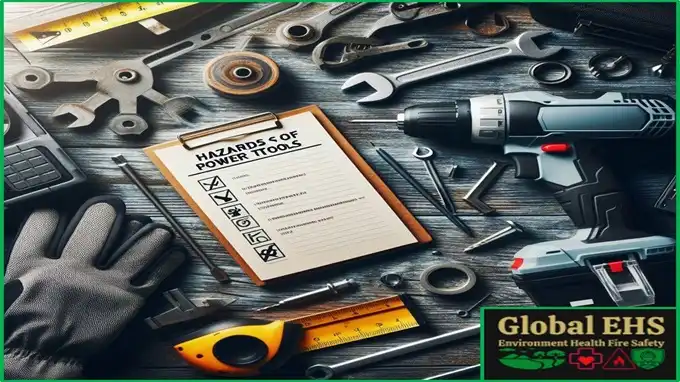
List of control measures and prevention tips from hazards of power tools;
1. Training and Education for hazards of power tools:
Provide comprehensive training on the safe operation of power tools, including proper handling, storage, and maintenance procedures.
2. Personal Protective Equipment (PPE):
Mandate the use of appropriate PPE, such as safety goggles, gloves, ear protection, and respiratory masks, to minimize exposure to hazards.
3. Equipment Inspection and Maintenance:
Conduct regular inspections of power tools to identify and address any defects or malfunctions promptly. Ensure proper maintenance and servicing to keep tools in optimal condition.
4. Tool Selection to avoid hazards of power tools:
Choose the right power tool for the job and ensure it is appropriate for the task at hand. Avoid using damaged or faulty tools and replace them when necessary.
5. Workspace Organization:
Keep the work area clean, clutter-free, and well-lit to reduce the risk of slips, trips, and falls. Provide adequate ventilation and implement proper storage solutions for power tools and accessories.
6. Safe Operating Procedures:
Develop and enforce safe operating procedures for using power tools, including guidelines for start-up, shutdown, and tool handling. Emphasize the importance of following manufacturer instructions and warnings.
7. Risk Assessment:
Conduct thorough risk assessments before using power tools to identify potential hazards and implement appropriate control measures. Consider factors such as environmental conditions, task complexity, and user experience.
8. Supervision and Monitoring for prevention of hazards of power tools:
Supervise users of power tools, especially inexperienced or novice operators, to ensure they adhere to safety protocols and best practices. Provide ongoing feedback and guidance as needed.
9. Emergency Preparedness:
Establish procedures for responding to accidents, injuries, or emergencies involving power tools. Ensure access to first aid supplies, emergency contact information, and evacuation routes.
10. Continuous Improvement to prevent and control of hazards of power tools:
Regularly review and update safety policies and procedures based on feedback, incident reports, and industry best practices. Encourage open communication and collaboration among workers to identify and address potential safety concerns.