Hazard and Operability Study (HAZOP)
Definitions and details:
HAZOP is defined as ‘The application of a formal systematic critical examination to the process and engineering intentions of the facilities to assess the hazard potential of mal-operation or malfunction of individual items of equipment and the consequential effects on the facility as a whole’.
In Hazard and Operability Study multidisciplinary team searches deviations form design intent though fixed sets of guide words or checklists or knowledge.
Conducting HAZOP can be to check the designs or operating procedures for a new project or an existing one. Conducting it can also be to improve safety implementing significant modifications or for other operational or legal reasons.
After carrying out the Preliminary Hazard Analysis (PHA) as explained earlier, the plant component, system or machine/equipment part which can cause ‘major hazard’ becomes known to us. Now to find out deviations or malfunctions leading to such event and its mode of operation, HAZOP helps us. Thus HAZOP is complimentary to PHA.
HAZOP study is carried out to determine deviations from normal operation and operational malfunctions which could lead to uncontrolled events.
Although development of the Hazard and Operability Study was to supplement experience-based practices when involvement of a new design or technology, its use has expanded to almost all phases of a plant’s life.
It is based on the principle that several experts with different background can interact and identify more problems when working together then when working separately and combining their results.
Therefore performance of HAZOP study by a multidisciplinary expert group always including workers familiar with the installation.
The examination procedure takes a full description of the process, systematically questions every part of it to discover how deviations from the intention of design can occur and decides whether these deviations can give rise to hazard.
Each part of design is analyzed with questions formulated around a number of guide words, which ensure that the question posed to test the integrity of each part of design will explore every conceivable way in which that design could deviate from design intention and then each deviation is considered for what the consequences it could lead to.
The potential hazards are noted for remedial action. Trivial or meaningless consequences are dropped out.
Stages at which Hazard and Operability Study can be carried out are:
- At an early stage of development to decide the site and identify major hazards.
- At design freeze stage i.e. when design is completed and construction is to be started.
- At Pre-start-up stage i.e. when construction is completed and the operation is to be started.
- Studies on existing plants.
- Studies prior to plant modification.
- Studies prior to taking a plant out of service.
- Studies on research facilities.
Procedure for HAZOP study follows the sequence:
- Define objective and scope.
- Select the team.
- Prepare for the study.
- Carry out the examination.
- Follow up.
- Record the results.
The objectives may be :
- to check a design.
- to decide whether and where to build.
- to decide whether to buy an equipment.
- to obtain a list of questions to put to a supplier.
- to check running instructions.
- to improve the safety of existing facilities etc.
- Composition of the team may be of Mechanical Engineer, Chemical Engineer, R & D Chemist, Production Manager, Project Manager, Instrument/Electrical Engineers, Civil Engineer etc. The team should not be too large. Head of the team may be by an experienced specialist form works management or by a specially trained consultant.
- After examining one part of the design and recording potential hazards if any, process the study to examine the next part of the design and repeat it until the whole plant has been studied.
The Preparative Work includes four stages
- Obtain the data.
- Convert the data into a suitable form.
- Plan the sequence for the study.
- Arrange the necessary meetings.
After discovery of a hazards, follow-up action becomes necessary. There may be a number of possible actions.
Generally they are of four types:
- Change in the process (material, recipe etc.)
- Change in process conditions (pressure, temperature, flow etc.)
- Alteration to the physical design including safety guarding.
- Change of operating methods.
While choosing between such possible actions, two categories become relevant:
- Those actions which remove the cause of hazard.
- Those actions which reduce the consequences.
Obviously the first category is first preferable. But then the study should be carry out at design stage to execute it at the minimum cost and better integrity.
Suppose the hazard is ‘sudden evolution of gas and pressure due to it’. Generally for this, four actions are possible:
- Change the material to eliminate the possibility of gas generation.
- Change the process condition (e.g. cooling, catalyst, low temperature, temperature control and cut off etc) to control the gas generation.
- Provide safety valve/rupture disc and vent for safe discharge.
- Provide personal protective equipment.
- Action-1 is 100 % effective and should be the first choice.
- Selection of Action-2 may be, if Action-1 is not possible and reliability of the control system is good.
- Selection of Action-3 may be, if Action-2 is not possible and effective only if design of the vent and dump-vessel can be deal to cope with the full discharge.
- Action-4 is the last resort if Action-1,2,3 are not possible or not effective.
Needs to do Recording containing:
1.Copy of the data as under:
- Process description, process flow diagram, material and enthalpy balances.
- Piping and instrumentation diagrams.
- Process equipment layouts – plan, elevation and section.
- Operating manual.
- Safety manual.
- Vendor information (P & I diagrams).
- Equipment specification sheets.
- Piping specifications.
- Plot plan.
- MSDS for materials.
- Any reports on safety reviews.
2. Marking of Copies of such documents by the team leader stating that their examination is complete.
Copy of all the working papers, questions, recommendations, redesigns etc. produces by the team and others as a result of the study.
Although, Retain file on the plant and prepare a report for the guidance of the managers.
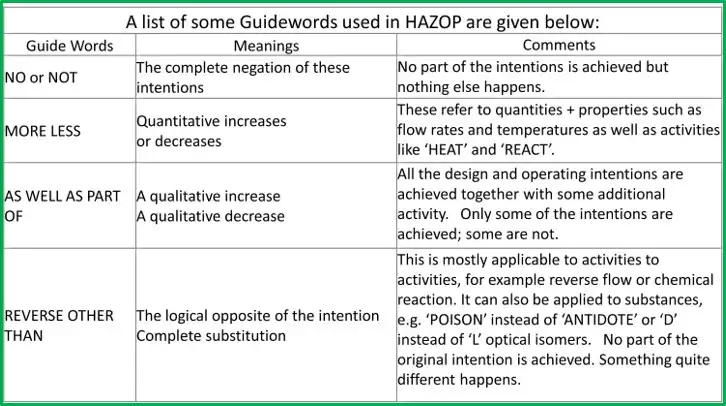
A sequence of Study proceeds as follows:

Various methods for HAZOP studies are described by DOW Safety Guide, HAZOP studies by ICL by Chemical Industry Safety and Health Council (CISHC), by Kletz, Gibbesen, Lawley and other expert. The basis of studies may be a word model, a process flow sheet, a plant layout, fault free technique etc.